Kon-Tiki - Die Demokratisierung der Pflanzenkohleproduktion
von Hans-Peter Schmidt & Paul Taylor
Please download here the citable PDF version of the article
Industriell hergestellte Pflanzenkohle wird in den nächsten Jahrzehnten vermutlich zu einem der entscheidenden Rohstoffe der biobasierten Wirtschaft. Da die Pflanzenkohle aber hauptsächlich in der Elektronik, der Bauindustrie, der Papierherstellung, der Abwasserreinigung und für sonstige neue Materialen im 3D-Druck verwendet werden wird, ist schon heute absehbar, dass industriell hergestellte Pflanzenkohle wohl zu teuer bleibt, um als bloßer Bodenverbesserer oder Güllezusatz in der Landwirtschaft zum Einsatz zu kommen. Die einzige Chance, kostengünstig Pflanzenkohle für den landwirtschaftlichen Einsatz zu erhalten, besteht darin, dass Landwirte und Gärtner ihre eigene Pflanzenkohle aus den eigenen vor Ort anfallenden Reststoffen herstellen. Nur dann kann Pflanzenkohle am Ende lokaler Nutzungskaskaden auch wieder zum Grundbaustein humusreicher Böden werden.
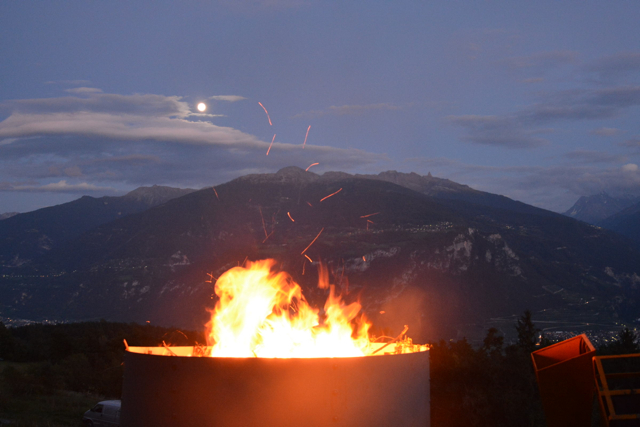
Die Völker aller alten Hochkulturen stellten Holzkohle in so riesigen Mengen her, dass ganze Länder entwaldet wurden. Hauptsächlich wurde diese Holzkohle zum Schmelzen von Erzen, zum Schmieden und zum Brennen von Keramik verwendet, doch ein nicht unerheblicher Teil wurde offenbar in Verbindung mit organischen Abfällen zur Verbesserung der landwirtschaftlichen Böden verwendet (Glaser and Birk, 2012).
Wenn nun aber die Völker vergangener Jahrhunderte Holz- und Pflanzenkohle in so großen Mengen herzustellen vermochten, wie kann es dann sein, dass es im Zeitalter der Hochtechnologie und nach inzwischen Millionen schweren Forschungsprojekten noch nicht gelungen ist, eine einfache, verlässliche und bezahlbare Anlage zu entwickeln, um auf Bauernhöfen und in Gemeinden aus den dort anfallenden Reststoffen wirtschaftlich rentabel Pflanzenkohle zu produzieren?
Wie haben unsere Vorfahren ohne Kettensägen, ohne Stahl, ohne Förderbänder und Elektromotoren so enorme Mengen Pflanzenkohle hergestellt, dass im Durchschnitt etwa ein Fünftel des Kohlenstoffs im Humus der weltweiten Böden Pflanzenkohle ist (Kluepfel et al., 2014; Rodionov et al., 2010; Schmidt and Noack, 2000). Auch wenn der Hauptteil dieser Pflanzenkohle im Humus durch natürliche, häufig wohl aber von Menschen veranlasste Wald- und Steppenbrände (Gammage, 2012; Gerlach et al., 2012; Rodionov et al., 2010) in die Böden gelangt ist, so muss doch im Umkreis von Siedlungsplätzen, wo der Anteil der Pflanzenkohle um ein weites den der sonstigen Böden übersteigt, die Pflanzenkohle aus gezielter Produktion stammen (Gerlach et al., 2012, 2006). Denn die kleinen Reste, die im Herdfeuer zurück bleiben, können die gefundenen Mengen (Glaser and Birk, 2012) nicht erklären.
Vom Feuer lernen
Wer je versucht hat, wenigstens hundert Quadratmeter wild gewachsenen Wald zu roden und pflügbar zu machen, der wird, selbst wenn er Kettensäge und Bagger zur Verfügung hat, sehr schnell einsehen, dass lediglich Feuer hilft, wenn man außer Steinaxt und Messer keine anderen Werkzeuge zur Hand hat. Feuer war für wenigstens 25.000 Jahre das wichtigste und allgegenwärtige Mittel aller jeder Kultur und aller Völker und Sippen, um sich in der Natur einen Platz zum Leben zu verschaffen. Nur durch die Nutzung von Feuer konnte der Mensch die Umwelt an seine Bedürfnisse anpassen und die ihm verfügbaren Ressourcen in einer Weise nutzen, die seine physischen und intellektuellen Vor- und Nachteile gegenüber der Tierwelt zu seinem Nutzen wenden.
Erst und nur das Feuer ermöglichte den Menschen, bevor sie die Umwandlung von Sonnenenergie und Biomasse in Strom erlernten, sich sicher und behaglich in ihrer Umwelt einzurichten. Wer aber täglich mit Feuer umgeht, jede Mahlzeit am Feuer bereitet, seine Werkzeuge und jeden Nagel daran schmiedet, Kalk brennt, Keramik schrüht, sich wärmt und seine Weiden und Wälder unterhält, der hat irgendwann gelernt, wie ein Feuer anzulegen ist, damit es maximale Wärme erzeugt und weder Haus noch Dorf in beißenden Rauch einhüllt: Ein rauchloses Feuer aber zündet man, anders als man intuitiv meint, von oben an und nicht von unten.
Die Analogie des Streichholzes
Anders als man wiederum intuitiv denkt (siehe hier das spannende Feld der intuitiven Physik), brennt Holz eigentlich nicht, sondern es brennt das Gas, dass beim Erhitzen von Holz ausdampft. Reibt man die Schwefelkuppe eines Streichholzes an der rauen Fläche der Streichholzschachtel, wird der Schwefel genug erhitzt, um sich zu entzünden. Der brennende Schwefel erzeugt sodann die Wärme, die das Holz des Streichholzes zum Ausgasen bringt, und das Gas an der Flamme des Schwefels entzündet. Es brennt dann also nicht das Streichholz, sondern das Holzgas, welches das Holz des Streichholzes immer weiter erhitzt, so dass es weiter ausgast und das Gas verbrennt. Unter der Flamme des Holzgases aber verkohlt das Holz, da die Flamme um das Streichholz herum allen Sauerstoff verbraucht, so dass unter dem Schutz der Flamme das Holz quasi unter Sauerstoffabschluss pyrolysiert. Wie man weiß, brennt das Streichholz mit sauberer Flamme, verkohlt in ihr, und beginnt erst zu rauchen und zu qualmen, wenn man es ausbläst, weil dann die Holzgase eben nicht mehr brennen, sondern bis zur vollständigen Abkühlung unverbrannt ausgasen.
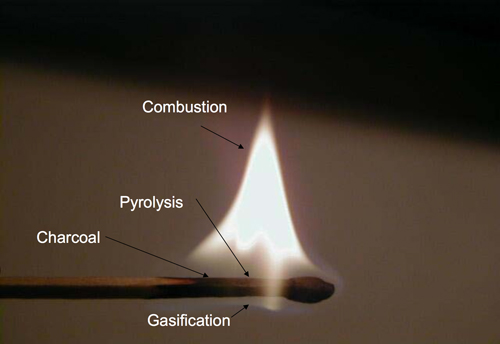
Und genau wie ein Streichholz funktioniert auch ein rauchloses Feuer, das man von oben entzündet, damit das Feuer in der obersten Schicht die nächst untere Schicht erhitzt und diese folglich auszugasen beginnt, wobei das Gas nach oben aufsteigt, von der darüber liegenden Feuerfront ergriffen wird und sauber verbrennt, anstatt qualmend zu verrauchen. Zündet man ein Feuer von unten an, beginnt zwar ebenfalls das darüber liegende Holz auszugasen, doch kann die Flamme nur einen Teil des aufsteigenden Gases erfassen. Anstatt vollständig abzubrennen, qualmt es in den Schornstein, ins Haus oder gar in die Kleider, Augen und Nasen der ums Feuer Sitzenden.
Zündet man hingegen einen geschickt locker geschichteten Holzhaufen mit genug kleinen Ästen oben an, muss alles entstehende Holzgas durch die jeweils darüber liegende Feuerfront, es kommt daher zu einer sauberen, rauchgasfreien Verbrennung. Unter der fast sauerstofffreien Feuerfront (nur von der Seite des Holzhaufens wird Luft angesaugt) verkohlt das Holz Schicht für Schicht nach unten. Die verkohlten Holzpartikel fallen durch den lockeren Haufen nach unten, so dass unter der Feuerfront beständig frisch ausgasendes Holz zu liegen kommt. Man muss den brennenden Haufen dann nur noch im richtigen Moment durch Wasser löschen oder mit Erde ersticken, und schon hat man anstatt Asche und rauchiges Feuer ein gutes Fünftel des Holzes zu Kohle pyrolysiert, und zuvor noch rauchlos gekocht, geschmiedet oder sich gewärmt.
Vom Grundprinzip rauchlosen Feuers
Die Überlegungen über dieses Grundprinzips des rauchlosen Feuers nahmen wir zum Ausgangspunkt zur Entwicklung des Kon-Tiki, eines nach oben hin offenen, konischen Meilers zur Herstellung von Pflanzenkohle. Den Namen Kon-Tiki wählten wir in Erinnerung an Thor Heyerdahl, dem in den 40er Jahren des letzten Jahrhunderts kein Wissenschaftler glauben wollte, dass Ureinwohner Südamerikas mit handgefertigten Booten den Pazifik bis nach Polynesien zu überqueren vermochten. Virulent griffen die Experten Heyerdahls Theorie an, bis er sie schließlich Verstummen ließ, als er eben solch ein Boot nur mit den Werkzeugen und Materialien der südamerikanischen Ureinwohner baute, und darin von Lima aus den halben Pazifik bis nach Polynesien überquerte. Sein Boot nannte er nach dem südamerikanischen Sonnen- und Feuergott: Kon-Tiki.
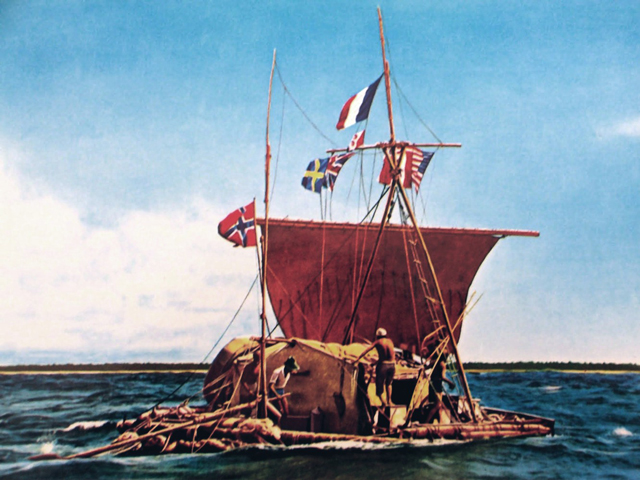
Unser Ziel war ganz ähnlich, wenn auch bei weitem nicht so abenteuerlich. Zum einen wollten wir nachvollziehen, wie unsere Vorfahren mit einfachsten Mitteln und ohne Hochtechnologie große Mengen Pflanzenkohle produzieren konnten. Und zum anderen suchten wir nach genau solch einer einfachen, kostengünstigen, überall adaptierbaren Technik für ein Terra Preta Projekt in Nepal. Dort, wie in vielen armen Regionen der Welt, wo Pflanzenkohle am meisten benötigt wird, können sich die Dörfer unmöglich eine unzuverlässige Hightech-Pyrolyse für eine halbe Million Dollar leisten. Wenn frühere Völker in Südamerika, in Australien, Skandinavien, Palästina, China, ja eigentlich fast überall auf der Welt solch unvorstellbare Mengen an Holz- und auch Pflanzenkohle herstellen konnten, dass ihre Böden teils durch und durch schwarz wurden, so muss dies doch auch heute selbst in den ärmsten tropischen Ländern gelingen können. Dass wir dabei auf eine Technologie stoßen würden, die es auch in den reichen Ländern den Landwirten und Gärtnern ermöglicht, ihre Pflanzenkohle viel günstiger selbst herzustellen, als sie von industriellen Herstellern zu kaufen, ahnten wir da noch nicht. Wir sind also gedanklich zunächst noch einmal zu den rauchlosen Feuern der Vorfahren zurückgekehrt und haben dies mit den Beobachtungen der Archäologen kombiniert, dass nämlich die Schwarzerde häufig in deutlich abgegrenzten Kegelformen mit einem oberen Durchmesser von 2 – 3 m und einer Tiefe von 1m50 in den Bodenprofilen zu finden ist (Eckmeier et al., 2008; Gerlach et al., 2006).
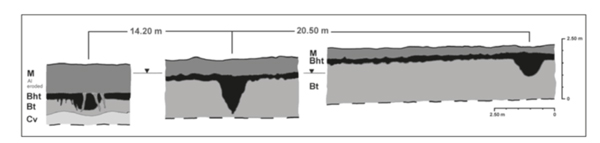
Zunächst vermuteten wir, dass diese ausgehobenen Erdkegel einfach Müllgruben waren, die, wenn sie aufgefüllt waren, von oben nach unten niedergebrannt wurden, um dann wieder aufgefüllt zu werden. In einigen Fällen wird das sicher auch so gewesen sein. Aber was, wenn diese knapp mannshohen Kohlegruben als gewollte „Gefäße“ zur Pyrolyse verwendet wurden, und die seitlich sowie nach unten geschlossene Form dieses „Feuerloches“ verhinderte, dass wie beim einfachen Scheiterhaufen sauerstoffreiche Luft von der Seite einströmen konnte? Dies galt es nun zunächst als experimentelle Archäologie zu testen!
Offene Erdmeiler
Sorgt man am Boden der Erdgrube durch ein Initialfeuer für ein kräftiges Glutbett, kann auf dieses nach und nach und Schicht auf Schicht brennbares Material wie Holz, Essenreste, Knochen, Blätter, Stroh usw. aufgeworfen werden. Die Gluthitze sorgt dafür, dass die aufliegende Biomasse ausgast und das so austretende Gas entzündet wird. Brennt das Pyrolysegas, verbraucht es allen Sauerstoff aus den darunter liegenden Schichten und verhindert damit quasi als Schutzgas, dass Sauerstoff von oben in die Pyrolysezone eindringen kann, während es von der Seite und von unten durch die Erdwände luftdicht gehalten wird. Das Feuer selbst also sorgt für den Luftabschluss nach unten, so dass die unter dem Feuer liegenden Schichten, anstatt zu verbrennen, ausgasen und verkohlen. Nach einigen Stunden entstehen so durch das stetige Aufschichten und Ausgasen frischer Biomasse einige Kubikmeter Pflanzenkohle. Will man diese Kohle nutzen, muss sie nur noch durch eine 5-10 cm dicke Erdschicht erstickt oder durch Wasser abgelöscht werden.
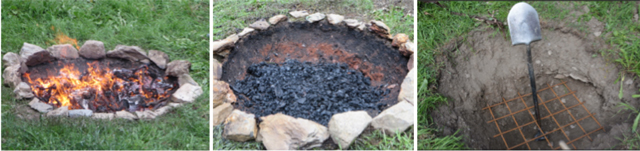
Inspiriert von Josiah Hunt (siehe hier ein Video über seine Methode) testeten wir zunächst die Produktion von Pflanzenkohle in einem offenen Erdmeiler. Und es funktionierte! Gleich im ersten Versuch stellten wir einige hundert Liter offenbar bester Pflanzenkohle in einem konisch ausgehobenen Erdloch her. Der Erfolg war Anlass genug, sich eingehendere Gedanken über das System des Erdmeilers zu machen und zu überlegen, wie sich das beschriebene Prinzip technisch umsetzen und steuern ließe.
Mit dem Feuer, nicht gegen das Feuer
Eine Recherche unter den Biochar-Kollegen der Welt ergab rasch, dass wir nicht allein auf dem Weg dieser Entwicklung waren. Auf ihrer höchst wertvollen Webseite Backyard Biochar präsentierte Kelpie Wilson bereits einige Beispiele wie den japanischen Moki-Kiln, den australischen Moxham Kiln, Kelpie Wilsons Pyramid Kiln oder Michael Wittmanns Cone Kiln. All diese Meiler (kiln) waren vergleichsweise klein, und eher für den Garten und Hobbybereich geeignet, aber das Prinzip war klar: Biochar mithilfe des Feuers und nicht durch Unterdrückung des Feuers herzustellen.
Auf Basis dieser grundlegenden Erkenntnis, die für die Pflanzenkohleproduktion quasi eine Kehrtwende von der gesamten modernen Pyrolysetechnik bedeutete, war der Weg zur Entwicklung eines optimierten, industriell standardisierbaren Kon-Tiki für die Produktion von qualitativ hochwertiger Pflanzenkohle in nennenswerten Mengen und zu außerordentlich günstigen Kosten quasi vorgezeichnet. Der Teufel freilich steckt im Detail, und es brauchte viel experimentelle Arbeit und theoretische Modelle bis wir uns schließlich den ersten optimal dimensionierten Modellen für höchste Kohlequalität bei geringsten Emissionen annäherten. Aber das Leitprinzip stand fest: Die Pyrolysegase als Schutzgas verwenden, und durch das Feuer selbst für Luftabschluss zur Pyrolysezone sorgen.
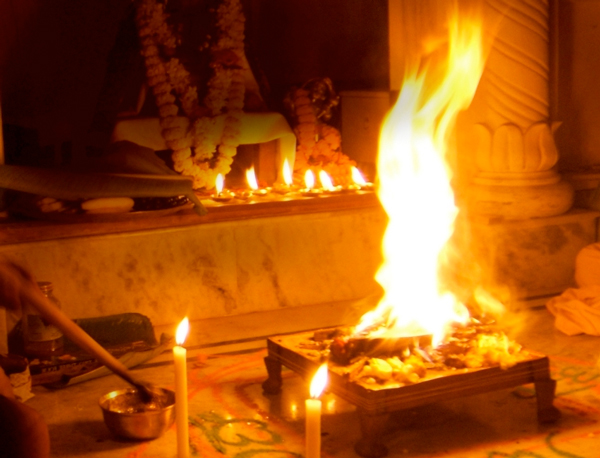
Kon-Tiki Kegelmeiler
Auch wenn die Kohlequalität aus den ersten Versuchen mit ausgehobenen Erdmeilern bereits recht gut schien, und die offene Verbrennung der Pyrolysegase ziemlich raucharm stattfand, so war die Kohlequalität zu inhomogen für standardisierbare Produkte und die Verbrennung schon bei leichten Windstößen zu instabil, um die Emissionen hinreichend unter Kontrolle zu bekommen. Wir mussten hier einen Schritt weiter gehen, um unter standardisierten Bedingungen die Funktionsprinzipen genauer zu untersuchen und die Parameter des Systems optimal aufeinander abzustimmen. So bauten wir den ersten 850 Liter großen Kon-Tiki aus Stahl.
Abb. 7: Der erste Versuchs Kon-Tiki hatte eine Durchmesser von 150 cm, eine Höhe von 90 cm und Fassungsvermögen von 850 l. Gebaut wurde er von Markus Koller.
Mit einem oberen Durchmesser von 1,50m, einer Höhe von 0,90m und einer Wandneigung von 60° wurde eine steile Kegelform gewählt, so dass sich das Kohlebett unterhalb der Feuerzone durch das Nachrieseln neu entstehender Kohlestücke gut verdichtet und die Feuerfront an der Oberfläche für einen zuverlässigen Luftabschluss sorgen kann. Das entscheidende Kriterium für den Erfolg der neuen Stahlform war allerdings, wie sich die Verbrennungsdynamik entwickeln würde, wenn die konische Form nicht mehr in den Boden eingelassen ist, sondern auf dem Boden steht. Anders als die Lehmwände im Erdmeiler reflektiert die Stahleinfassung die Pyrolyse- und Verbrennungswärme zurück in den Meiler, was eine gleichmäßigere Temperaturverteilung und damit eine homogenere Verkohlung und Kohlequalität garantiert. Als noch wichtiger erkannten wir allerdings, dass die von oben in den Meiler hineingesogene Verbrennungsluft zunächst außen an den heißen Außenwänden des Kon-Tiki aufsteigt, wodurch sie erwärmt wird. Dies verringert die Abkühlung der zu verbrennenden Gase deutlich und erzeugt eine stabile Verbrennungsdynamik, die die Rauchentwicklung stark reduziert.
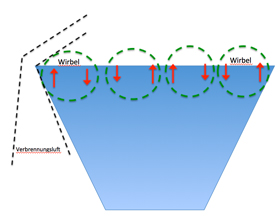
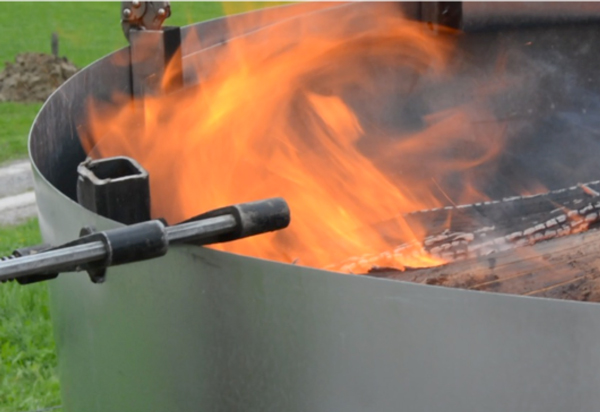
Optimierung der Verbrennung durch Verwendung eines Außenmantels
Zur weiteren Optimierung der Verbrennungsdynamik wurde der Kon-Tiki mit einem dünnen metallischen Mantel umgeben, so dass zwischen den geneigten Wänden des Meilers und dem äußeren Mantel die Verbrennungsluft stärker erwärmt wird. Der Mantel ragt knapp zehn Zentimeter über den Rand des Meilers, wodurch zum einen verhindert wird, dass kalte Verbrennungsluft direkt in den Meiler gesaugt wird und zum anderen, dass etwaige Windstöße die Verbrennungsdynamik stören. Tatsächlich gleitet die dichtere kalte Luft von der Außenseite des Mantels auf der vorgewärmten Luft aus dem Zwischenraum von Meiler und Mantel, was außerordentlich stabilisierend wirkt und verhindert, dass Rauch oder gar Feuer seitlich aus dem Kon-Tiki ausbrechen können. Ein weiterer Vorteil des Mantels besteht darin, dass die Kon-Tiki-Innenwand nicht durch die Außenluft oder gar durch Windstöße gekühlt wird, was die Reflexionsleistung ins Innere der Pyrolysezone verbessert. Zudem schützt es die Arbeiter vor etwaigen Verbrennungen. Tatsächlich erwärmt sich der Mantel nur im aller obersten Bereich auf maximal 60°C.
Trocknen und Pyrolysieren
Wie schon bei den offenen Erdmeilern beobachtet, trocknet die Feuerfront an der Oberfläche rasch die nachgelegte Biomasse, so dass dank der enormen, bei der Pyrolyse frei werdenden Trocknungsenergie auch feuchte Biomassen problemlos verkohlt werden können. Hat sich erst einmal ein energiereiches Glutbett am Boden des Kon-Tikis gebildet, kann sogar frisch geschnittenes Holz, Laub oder auch Viehmist pyrolysiert werden. Entscheidend ist, dass der Kon-Tiki genügend Energie zur raschen Verdampfung des Wassers freisetzt. Der Kon-Tiki funktioniert also zugleich als Trockner und als Pyrolysator. Gegenüber den meisten geschlossenen Pyrolysesystemen ist allein dies schon ein großer Vorteil.
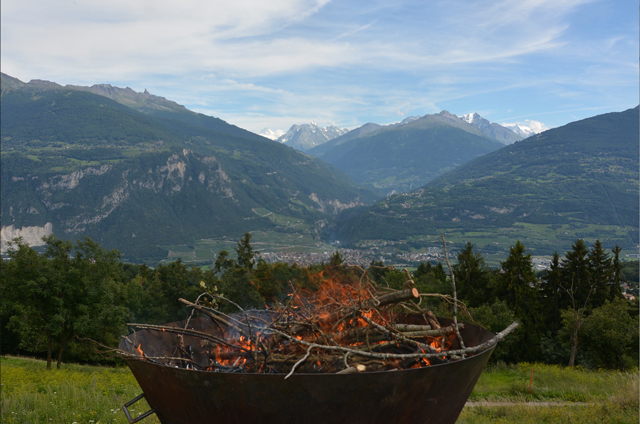
Entzünden und Nachschichten
Beim ersten Versuch des Anfeuerns im ziemlich tiefen Kon-Tiki fürchteten wir schon, dass es nicht funktionieren würde, denn tief unten im Stahlbehälter ist der Sauerstoff sehr schnell aufgebraucht. Tatsächlich war es zunächst unmöglich, auch mit noch so gutem Zündholz ein Feuer zu entfachen. Nach einigen Versuchen und Überlegungen fanden wir aber eine höchst praktikable Anfeuerungstechnik, die uns noch immer jedes Mal aufs Neue begeistert.
Man baut dazu in der Mitte des Meilers bis auf eine Höhe von etwa drei Viertel einen hölzernen Kamin aus möglichst trockenem Scheitholz, das dafür viereckig ineinander gestapelt wird. Dieser luftige Holzkamin wird mit etwas Zunder oben angezündet. Wenn die obersten beiden Reihen des Kamins gut brennen, entsteht ein Zug, der innen an den Seitenwänden des Meilers Luft nach unten und im Kamin wieder nach oben zieht. Stellt sich dieser Effekt nach knapp zehn Minuten ein, stößt man das brennende Holz von oben den Kamin hinab, so dass sich der Fuß des Holzkamins entzündet. Nach weiteren rund fünf Minuten kann der „Kamin“ dann zusammengestoßen und gleichmäßig am Boden ausgebreitet werden.
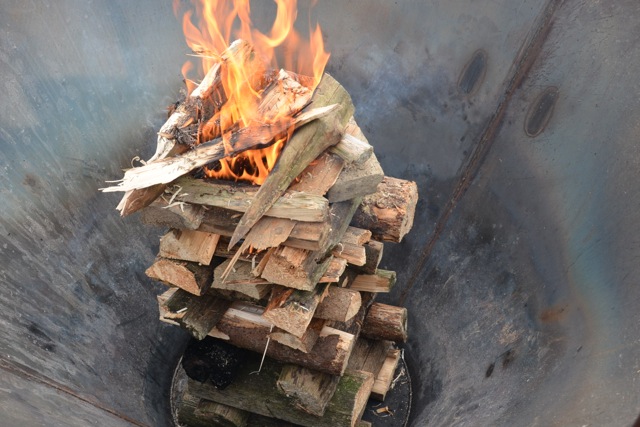
Weitere fünf bis zehn Minuten später hat sich ein ausreichend heißes Glutbett gebildet, und die Oberflächenschicht beginnt sich mit weißer Asche zu überziehen. Dies ist der Moment, um die erste Biomasseschicht aufzulegen. Sie sollte möglichst gleichmäßig die Glutzone bedecken und auf keinen Fall zu dick sein. Sobald sich diese neue Biomasseschicht ebenfalls mit weißer Asche überzieht, ist dies das Zeichen, dass das meiste Holzgas entwichen ist und die entstandene Kohle zu glimmen beginnt, so dass die nächste Biomasseschicht aufgeschichtet werden kann. Dieser Vorgang des Nachlegens wird alle fünf bis zehn Minuten bis zum Ablöschen wiederholt. Die Arbeit mit dem Kon-Tiki bedarf folglich die beständige Präsenz einer Person, die geschickt frische Biomasse nachlegen muss. Verpasst man den richtigen Zeitpunkt, beginnt die Kohle zu verglühen, wodurch sich der Ascheanteil der Kohle erhöht. Schichtet man zu schnell zu viel Biomasse auf, genügt das Feuer nicht, um alle Pyrolysegase einzufangen und es kommt zu Rauchentwicklung.
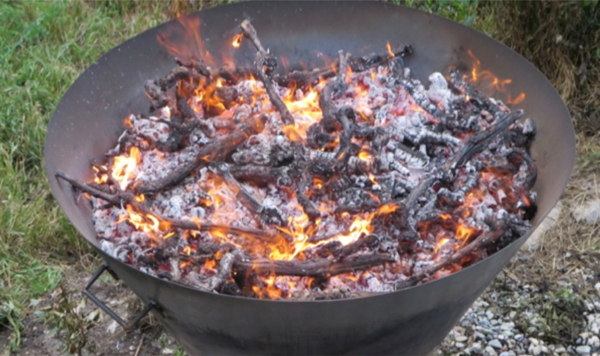
Feuerungsdauer
Im Vergleich zu einer automatisierten Anlage besteht der Nachteil des Kon-Tikis also darin, dass er während der gesamten Dauer von Hand beliefert werden muss. Je nach Art, Stückigkeit und Wassergehalt der verwendeten Biomasse dauert es zwei bis acht Stunden, um mit einem größeren Kon-Tiki 1 m3 Pflanzenkohle herzustellen. Verwendet man trockene Holzhackschnitzel, dauert es nur knapp zwei Stunden, ungetrockneter Rebschnitt dauert vier bis fünf Stunden, frisches Baumholz mit Scheiten, Ästen und Blättern dauert bis zu acht Stunden. Wiederum je nach Biomasse kann eine Person zwei bis vier Meiler parallel bedienen. An einem Arbeitstag kann eine Person also gut ein bis anderthalb Tonne Pflanzenkohle herstellen, was in etwa der Tageskapazität (also 24h im kontinuierlichen Betrieb) von mittelgroßen technischen Pyrolyseanlagen entspricht.
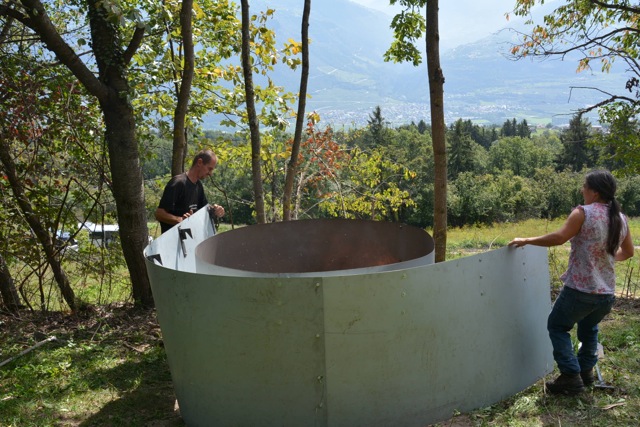
Ein weiterer Vorteil des Kon-Tiki besteht darin, dass die Biomasse nicht homogenisiert, gehäckselt oder gar pelletiert werden muss, sondern einfach grob und bis zu 120 cm lang aufgeschichtet werden kann, auch wenn die Verkohlungszeit dadurch um einiges länger ist als mit trockenen, kleinstückigen Biomassen. Bei der Verwendung von frischen Zweigen und Ästen entspricht die Größe eines Kon-Tiki etwa der Menge an Biomasse, die in acht Stunden bei der Landschaftspflege oder beim Schnitt von Feuerholz anfällt. Anstatt die für Feuerholz ungeeigneten Äste und das Gestrüpp auf einen lange nicht verrottenden Haufen zu werfen, kann man es quasi nebenbei im Kon-Tiki verkohlen.
Ablöschen
Der Kon-Tiki darf nur bis maximal 10 cm unter dem oberen Rand befüllt werden, da sonst die stabile Gas-Luft-Verwirbelung gestört und die Verkohlung der oberen Schichten inhomogen wird. Ist der Kon-Tiki also nahezu gefüllt, legt man die letzten zwei bis drei Schichten nur noch rasch verkohlendes Material wie dünne Äste oder Rebschnitt auf, da größere Stücke in der Endphase entweder unverkohlt bleiben oder für zu großen Abbrand und Asche sorgen würden.
Etwa 20 Minuten bevor die letzte Schicht pyrolysiert ist, wird der Wasserzufluss am Boden des Kon-Tiki geöffnet. So strömt langsam von unten Wasser in den Meiler. Trifft das Wasser auf die heiße Kohle, verdampft das Wasser. Der sich schließlich bis auf 700°C erhitzende Wasserdampf steigt durch das Kohlebett auf und sorgt nicht nur für eine langsame Ablöschung, sondern aktiviert die Pflanzenkohle. Durch den heißen Wasserdampf werden Kondensate aus den Poren der Pflanzenkohle ausgetrieben. Die Pflanzenkohle wird so quasi geputzt, womit das Porenvolumen und die innere Oberfläche der Kohle zunehmen. Auf diese Weise entsteht teilaktivierte Pflanzenkohle (Aktivkohle) mit Oberflächen von weit über 300 m2 pro Gramm, was höher ist, als es in den geschlossenen Systemen technischer Anlagen erreicht wird.
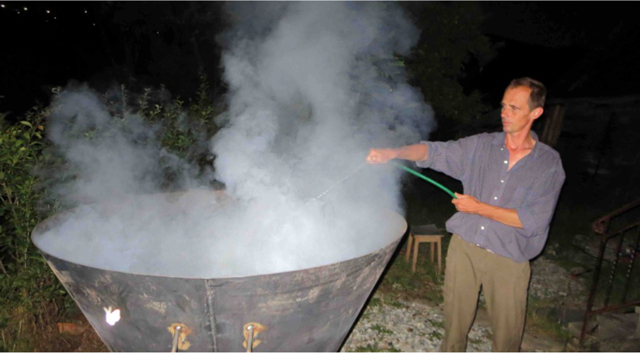
Das Feuer in der obersten Schicht des Kon-Tiki wird durch den Wasserdampf nicht gelöscht, weil die oberste etwa 20 cm dicke Glutzone so mit heißem Pyrolysegas gefüllt ist, dass sie auf dem steigenden Wasser aufschwimmt. Bemerkt man, dass die letzte Kohleschicht aufzuschwimmen beginnt, spritzt man diese von oben mit Wasser ab und löscht damit den Meiler komplett. Alternativ kann man den Meiler auch gänzlich von oben ablöschen, wobei sich allerdings der Effekt der Dampfaktivierung, wie er durch die Wässerung von unten entsteht, nicht einstellen kann. Das Porenvolumen und die spezifischen Oberflächen der Pflanzenkohle sind dann entsprechend kleiner. Möchte man die Kohle nicht nässen, sondern später z.B. als Grillkohle verwenden, kann man den Meiler entweder mit einem luftdichten Deckel schließen oder einfach Erde aufwerfen. Die durch Trockenlöschung entstehende Pflanzenkohle ist allerdings reicher an Kondensaten und auch Schadstoffen wie PAK. Für Grillkohle mag dies gut sein, da die Kondensate und Schadstoffe gut brennen, aber für den Einsatz in der Tierhaltung ganz gewiss nicht.
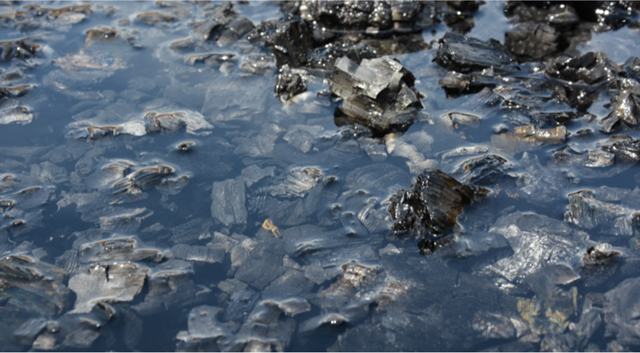
Das Löschwasser, welches auch Quenchwasser genannt wird, kann man einige Stunden oder auch Tage im Meiler belassen. Durch den unteren Abfluss lässt es sich leicht ablassen. Das Quenchwasser ist sauber und transparent, aber seifig und hat einen recht hohen pH-Wert. Während der hohe pH-Wert auf die ca. 10% bei der Pyrolyse ebenfalls entstehende Asche zurückzuführen ist, entsteht die Seife durch die Reaktion der Asche mit Pyrolyseölen, die beim Dämpfen der Kohle aus den Poren ausgetrieben werden. Dieses seifige Quenchwasser eignet sich offenbar hervorragend zum Gießen von Obst- und Gemüsepflanzen, vertreibt Schnecken und Pilze und wirkt allgemein kräftigend auf die Pflanzen. Letztere Aussage beruht jedoch bisher nur auf eigenen Beobachtungen mit zwei Dutzend Pflanzenarten, systematische wissenschaftliche Untersuchungen stehen noch aus.
Qualität
Kon-Tiki Pflanzenkohle, die mit Wasser abgelöscht wird, erfüllte nach bisherigen Untersuchungen alle Ansprüche an die Premiumqualität des Europäischen Pflanzenkohle Zertifikates (EBC). Das offene Pyrolyseprinzip garantiert, dass der allergrößte Teil der Pyrolysegase aus der Kohle ausgetrieben und verbrannt wird, also nicht in Form von teils toxischen Kondensaten die Kohleoberflächen und Poren verklebt. Durch die langsame Ablöschung mit Wasserdampf wird die Pflanzenkohle noch zusätzlich gereinigt und aktiviert. Unter folgendem Link finden Sie die Analysedaten einer Kon-Tiki Pflanzenkohle.

Die Pyrolysetemperatur liegt im Kon-Tiki bei etwa 650-700°C mit kurzzeitigen Temperaturspitzen bis zu 800°C. In diesem Temperaturbereich wird die Biomasse einschließlich ihres Ligninanteils vollständig verkohlt. Es entsteht eine Hochtemperaturkohle von hoher Qualität, die sich insbesondere in der Tierhaltung als Zusatzstoff für Futtermittel, als Einstreu, zur Güllebehandlung, für die Kompostierung, zur Trink- und Abwasserbehandlung und allgemein zur Bindung von Toxinen und flüchtigen Nährstoffen eignet. Weniger geeignet ist die Kon-Tiki-Pflanzenkohle zum direkten Einsatz im Boden, da sie als Adsorber vermutlich die labilen Nährstoffe des Bodens und Signalstoffe von Pflanzen binden würde. Vor dem Einsatz als Bodenverbesserer muss die Pflanzenkohle aus dem Kon-Tiki also unbedingt zunächst mit Nährstoffen aufgeladen werden.
Zukunft
Die Verkohlung mit dem Kon-Tiki funktionierte vom ersten Versuch an besser, als wir es uns auch nur ansatzweise hätten träumen lassen. Trotzdem war längst nicht alles so einfach, wie es im Nachhinein scheint. Was es uns aber leicht gemacht hat, die unzähligen Versuche zur Optimierung der Form und Dimensionen durchzuführen und die thermodynamischen Rätsel zumindest ansatzweise zu knacken, war die grandiose Freude, unmittelbar mit dem Feuer zu arbeiten. Jeder Versuch dauerte mindestens sechs, meist jedoch acht bis zehn Stunden draußen am Waldrand, auf den Terrassen der Urahnen, im Angesicht der Berge. Manchmal luden wir Freunde ein, oft waren die Kinder dabei, die längst Feuer- und Biochar-Experten geworden sind. Es war der schönste Sommer: archäologische Zukunfts-Forschung am offenen Feuer. Wir haben gefilmt, fotografiert, unzählige Messungen durchgeführt, und neue Messtechniken erlernt.
Freundschaften haben sich am Feuer und beim Teilen der auf dem Kon-Tiki gekochten Mahlzeiten gefestigt. Es ging uns wie vielen unserer Vorfahren, wir haben mit den Kräften der Urelemente experimentiert und dabei die Ehrfurcht vor der Natur auf neue Weise entdeckt. Im Zeitalter der Hochtechnologie haben wir diese für einen Moment hinter uns gelassen, um wie Thor Heyerdahl auf seinem Floß im Meer an einigen Grundfesten der wissenschaftlichen und technischen Einbildung zu rütteln. So wie das Wunder alternden Weines auf dem dosierten Einfluss der Luft beruht, jenem Feind der Oenologen, so basiert die Qualität der Kohle, die unsere Böden letztlich wieder zu Schwarzerde machen könnte, auf dem dosierten Einsatz von Luft und Feuer.
Das erste Video, das wir im Juli 2014 auf youtube veröffentlicht haben (siehe oben), hat in Windes Eile viele Menschen in aller Welt erreicht. Für uns war von Beginn an klar, dass wir das Design ohne Patentschutz als open source Quelle zur Verfügung stellen würden. Trotzdem haben wir mit der eigentlichen Veröffentlichung eines Artikels über die Kon-Tiki Technik bis Ende des Herbst 2014 gewartet, um mehr Kenntnisse über die Funktionsprinzipien zu sammeln, das Design zu optimieren, und vor allem um mehr Sicherheit über die Qualität der Kohle, die Massenbilanzen und die Emissionen zu gewinnen.
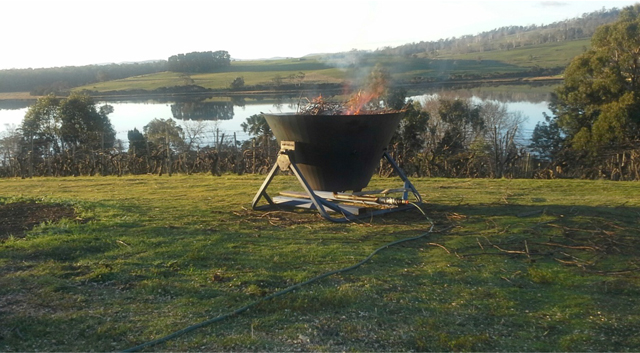
Auf Basis des Videos und der gleichwohl bereits von uns zur Verfügung gestellten Konstruktionsunterlagen wurden bis November 2014 bereits Kon-Tikis in Australien, Irland, Kanada, Kalifornien, England, Ungarn, der Schweiz und Südafrika nachgebaut. In Nepal, Indien, Indonesien, auf Hawai, in Deutschland und Malawi sind derzeit weitere Kon-Tikis im Bau. Da an allen Orten, wo der Kon-Tiki bereits Pflanzenkohle produziert, die Begeisterung offenbar riesig ist, und nirgendwo Komplikationen aufgetreten sind, gehen wir davon aus, dass 2015 hunderte Kon-Tikis überall auf der Welt die Demokratisierung der Pflanzenkohleproduktion einläuten werden.
Ursprünglich für die Landwirtschaft in Entwicklungsländern konzipiert, zeigt sich mehr und mehr, dass ebenso in Europa, Australien und Amerika Landwirte und einige andere die Chance ergreifen, ihre Pflanzenkohle selbst herzustellen und mit ihrer Nutzung die landwirtschaftlichen Stoffkreisläufe zu optimieren. Schließlich ist die eigene Herstellung von Pflanzenkohle wahrscheinlich der einzige Weg, um sie mit wirtschaftlichem Erfolg in der Landwirtschaft einsetzen zu können, dezentral, wie es dem Wachstum von Biomasse auf unserem Planeten entspricht.
Nächste Entwicklungsschritte
Mit zahlreichen Partnern in verschiedenen Ländern arbeiten wir derzeit an der Optimierung der Geometrie und Thermodynamik des Kon-Tiki. Für eine amerikanische Universität haben wir jüngst einen Forschungs-Kon-Tiki entwickelt, mit dem sich sämtliche Parameter überwachen und durch Dosierung der Luftzufuhr die Verbrennung steuern und messen lässt. Für ein Kompostwerk wurde ein Riesen-Kon-Tiki gebaut, um große Wurzelstöcke mit minimaler Zerkleinerung zu verkohlen. Zudem entwickeln wir derzeit kleiner dimensionierte Kon-Tikis für Hausgärten, um direkt vor Ort anfallenden Grünschnitt und organische Abfälle zu Pflanzenkohle zu verarbeiten und die Grillsaison zu bestreiten – mit Kohleproduktion statt Kohleverbrauch.
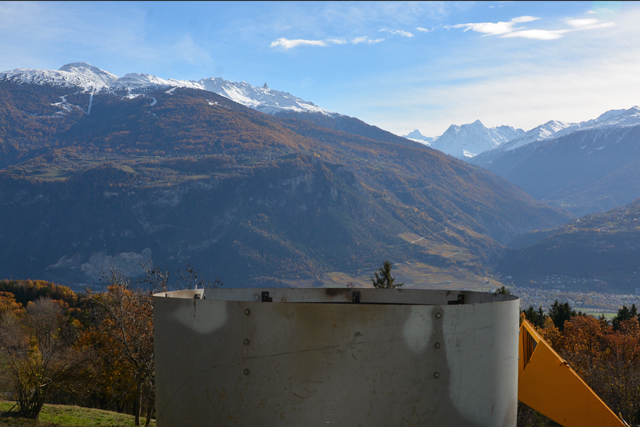
Der nächste technische Entwicklungsschritt wird die Integration einer Wärmerückgewinnung sein, denn die entstehende Wärme einer Kon-Tiki Feuerung beträgt mehr als 1 MWh, womit ein schlecht isoliertes Bauernhaus zwei Wochen lang geheizt werden könnte. Diese und weitere Entwicklungen, wie z.B. die Automatisierung des Kohleaustrages, werden Gegenstand weiterer Artikel sein. Aktuelle Informationen, Anleitungen und Videos über neuste Versuche finden Sie auf der Webseite des Ithaka-Instituts.
Das Geniale des Kon-Tikis sind die Eleganz der einfachen Form und die Vermeidung teurer beweglicher Teile und Steuerungen. Dadurch ist der Kon-Tiki robust und kostengünstig. Trotzdem glauben wir nicht, dass sich die Kon-Tiki Technologie für professionelle Unternehmen zur Herstellung großer Mengen Pflanzenkohle lohnen wird; hier bleiben automatisierte, kontinuierlich betriebene Anlagen mit geringem Personalaufwand unübertrefflich. Aber für kleinere und mittelgroße Landwirte, für Landschaftspfleger, für Winzer (Rebschnitt) und Kleingärtner, die gelegentlich ihre eigene qualitativ hochwertige Pflanzenkohle herstellen wollen, wird es kaum etwas Effizienteres, Preisgünstigeres und zugleich Schöneres geben.
Bauen oder Kaufen und eine Spende für Forschung und Entwicklung
(1. August 2016): Seit der Veröffentlichung dieses Artikels wurde der Kon-Tiki in über 50 Ländern in verschiedensten Formen und Weiterentwicklungen gebaut. Mehrere Firmen haben Kon-Tiki-Systeme auf den Markt gebracht. Während Kon-Tikis für professionelle Farmer einen Kubikmeter Kohle pro Stunde erzeugen und effizient die Restwärme zurückgewinnen, können Kleingärtner auf ihrem 150 l Garten Kon-Tiki komfortabel grillen. Wer nicht in optimierte Komplettsysteme aus Stahl mit Dampfablöschung und Vorwärmung der Verbrennungsluft investieren möchte, kann sich mit unserer Bauanleitung auch einen einfachen Erd-Kon-Tiki selbst graben oder einen alten Waschzuber umfunktionieren. Sofern dabei die Grundprinzipien eines stabilen Flammenteppichs über der zu verkohlenden Biomasse beachtet, wird Pflanzenkohle mit hervorragender Qualität erzeugen. Wer sich selbst einen Kon-Tiki schweißen oder in seiner Region die Produktion von Kleinserien aufbauen möchte, dem helfen wir gern im Tausch gegen eine Spende für die Unterstützung unserer Forschung mit technischen Zeichnungen und einer Bauanleitung. Zahlreiche weitere Informationen über und rund um den Kon-Tiki und die daraus gewonnene Pflanzenkohle finden Sie auf der Webseite des Ithaka Instituts.
Die gesamte Entwicklungsarbeit des Kon-Tiki hat das Ithaka Institut aus eigenen Mitteln bestritten, was uns an die Grenzen unserer finanziellen Möglichkeiten brachte. Da wir das Design den Landwirten der Welt frei und ohne Patentschutz zur Verfügung stellen, können wir auch keine finanziellen Gewinne aus dieser Arbeit ziehen. Aus diesem Grund geht hiermit auch an Sie, liebe Leser, die Bitte, unsere Arbeit mit einer Spende an das Ithaka Institut zu unterstützen, so dass wir die Forschung für die Weiterentwicklung des Kon-Tiki und die Demokratisierung der Pflanzenkohle-Produktion fortsetzen können. Finden Sie hier die Möglichkeit zur Überweisung Ihre Spende für die Entwicklung des Kon-Tiki.
Literatur
Eckmeier, E., Gerlach, R., Tegtmeier, U., Schmidt, M.W.I., 2008. Charred organic matter and phosphorus in black soils in the Lower Rhine Basin (Northwest Germany) indicate prehistoric agricultural burning. In: Fiorentino, G., Magri, D. (Eds.), Charcoals from the Past: Cultural and Palaeoenvironmental Implications. Oxford, pp. 93–103. Gammage, B., 2012. The Biggest Estate on Earth. Allen&Unwin, Sydney, Melbourne, Auckland, London. Gerlach, R., Baumewerd-schmidt, H., Borg, K. Van Den, Eckmeier, E., Schmidt, M.W.I., 2006. Prehistoric alteration of soil in the Lower Rhine Basin , Northwest Germany — archaeological , 14 C and geochemical evidence 136, 38–50. Gerlach, R., Fischer, P., Eckmeier, E., Hilgers, A., 2012. Dark soil horizons and archaeological features in the Neolithic settlement region of the Lower Rhine area , NW Germany : Formation , geochemistry and chronostratigraphy. Quat. Int. 1, 191–204. Glaser, B., Birk, J., 2012. State of the scientific knowledge on properties and genesis of Anthropogenic Dark Earths in Central Amazonia ( terra preta de Índio). Geochim. Cosmochim. Acta 82, 39–51. Kluepfel, L., Keiluweit, M., Kleber, M., Sander, M., 2014. Redox properties of plant biomass-derived black carbon (biochar). Environ. Sci. Technol. Rodionov, A., Amelung, W., Peinemann, N., Haumaier, L., Zhang, X., Kleber, M., Glaser, B., Urusevskaya, I., Zech, W., 2010. Black carbon in grassland ecosystems of the world. Global Biogeochem. Cycles 24. Schmidt, M.W.I., Noack, A.G., 2000. Black carbon in soils and sediments: Analysis, distribution, implications, and current challenges. Global Biogeochem. Cycles 14, 777–793.
A.Schlauch
27.11.2014 12:14
Hallo Hans-Peter,
schön mal wieder etwas hier zu lesen und dann gleich solch feiner Artikel. Ein sehr guter Ofen, der den richtigen Weg markiert für eine ernsthafte Low-Tech-Massenanwendung! Da lacht mein Töpferherz, an keiner Stelle macht meine Intuition und Erfahrung Fragezeichen oder Widersprüche. Top-Topf, der auch fit sein sollte fürs Keramikbrennen(locker bis 1000°)! Ich denke, das wird ein echter Klassiker.
Ich melde schon mal Interesse für eines der guten Stücke aus der ersten Kleinserie an.
beste Grüße
Andre
Markus Lanfranchi
28.11.2014 09:55
Lieber Hans-Peter
vielen Dank für diese exzellente Anleitung. Speziell für unsere eher abgeschiedenen Landwirtschaftsflächen die dringend einen Energieschub vertagen könnten, eignet sich diese dezentrale Methode wohl bestens. Ich freue mich nicht nur auf die Fruchtbarkeitssteigerung sondern auch auf das Feuer-Ritual!
Der Text über unseren finanziellen Reichtum bei gleichzeitigem Verlust des Glücks der Selbstbestimmung hat mich sehr berührt.
Herzlich aus dem Südosten
Markus
Daniel Nägeli
29.11.2014 15:55
Herzlichen Dank für diesen ausgezeichneten Artikel! Ich habe mich immer gefragt, wie man die Bioholzkohle selber herstellen statt von Hightech-Anlagen einkaufen kann.
Genau so sollte Forschung gemacht werden: auf die praktische Nutzbarkeit für die Menschen aller Länder ausgerichtet, und unter Einbezug der bisherigen Erkenntnisse überall auf der Welt. Ich glaube fest, dass es nicht umsonst ist, die Forschungsergebnisse offen zur Verfügung zu stellen. Denn viele, die sie nutzen, werden ihren Wert erkennen und nach ihren Möglichkeiten etwas zurückgeben oder zur Verbesserung beitragen.
Ich bin gespannt auf die kleinere Version für den Hausgarten (wie gross ist nötig für die effiziente Verkohlung?), und gehe davon aus, dass diese die bisher verbreitete Feuerschale ablösen wird.
Herzlich
Daniel
Thomas Rippel
30.11.2014 10:33
Lieber Hans-Peter
Ich möchte dir gratulieren zu dieser Innovation. Hut ab! Das ist ein echter Meilenstein.
Habt ihr die genauen Baupläne auch hochgeladen?
Gruss
Thomas
hps
30.11.2014 11:29
Salut Thomas, wir möchten in dieser Anfangszeit gern noch ein bisschen die Hand auf der Entwicklung behalten und auch die Ergebnisse sehen von möglichst vielen, die Kon-Tikis bauen und Pflanzenkohle damit produzieren. Daher bitten wir um persönliche Kontaktaufnahme für die Übergabe der Baupläne. Was wir dann auch gern nutzen zur Aufforderung für eine bescheidene Spende, die uns hilft weiter solche Technologien open source zu entwickeln. Schönen Gruss, Hans-Peter
Ueli Blatter
01.12.2014 08:24
alles Geniale ist einfach, man muss es nur finden - toll, eine Revolution! Endlich kann ich vernünftig Kohle selber herstellen.
Ich möchte mir ev. zusammen mit Freunden eine Kon Tiki bauen und in Frankreich, sowie in der Schweiz einsetzen und Terra preta fördern. So wird Terra preta Substrat erschwinglich. Neben TP wird Kon Tiki auch zu einem sozialen Projekt.
bitte senden sie mir die Baupläne zu. Für jede Benützung werde ich Ihnen einen wohlverdienten Obulus zustellen.
herzlich Ueli Blatter, Naturgärtner
Ueli Scheuermeier
02.12.2014 13:00
Leute, Leute, wisst ihr was ihr da anstoesst? Das ist riesig! Vielen Dank.
Emmental Forest Cooperation EFCO arbeitet mit afrikanischen Kleinunternehmern in abgelegenen laendlichen Gegenden von Tanzania. Das Land hat ein "big dirty energy secret", will sagen: Der Holzkohleverbrauch fuers Kochen ist landesweit so hoch und steigend, dass bis in 30 Jahren kein Baum mehr stehen duerfte. Gleichzeitig brennt die Savanne in riesigen Flaechen jedes Jahr ab. Das hohe duerre Gras und Staudengestruepp setzt oft riesige Mengen an Energie frei und ist eine Gefahr fuer gepflanzte Baeume und generell fuer den rasch schwindenden Wald - die Energie muesste man nutzen koennen!
Frage: Wird es moeglich auch "Stroh" oder gar "Strohhaecksel" mit dem Kon-Tiki zu verkohlen? Wisst ihr das schon, oder muesste man das erst noch ausprobieren? Falls ja, dann sehe ich Teams von jungen Leuten ueber Monate hinweg solche Kon-Tikis fahren und Graskohlestaub an Pressanlagen liefern und sich so ein Einkommen sichern. Der Kohlestaub wuerde dann zu Briketts gepresst als Alternative zur Baum-basierten Holzkohle welche gegenwaertig gebraucht wird (spaeter sehe ich auch Vergasung von solchen Briketts zwecks Betreiben von Traktoren, Generatoren, usw).
Ist diese Vision denkbar?
Ueli
hps
02.12.2014 13:28
Wissen, wissen wir nicht, aber hoffen schon. Jedenfalls habe ich's vor dem inneren Auge, was daraus werden könnte. Bei der Strohpyrolyse kommte kommt es ein bisschen auf die Grasart und den Asche- bzw. Energiegehalt an. Je nach dem brauch man +/- 30% Holzabfälle dazu. Aber genau die wären ja durch das Staudengestrüpp gegeben. Gemeinsam mit diesen Büschen wird es sehr gut funktionieren und hervorragende Kohle ergeben. Wenn man dann noch einen Schritt weitergeht und wenigstens einen Teil der Pflanzenkohle abzweigt, um sie beim Baumpflanzen ins Pflanzloch zu geben (aufgeladen mit Mist/Urin), dann könnte man auch wieder die Aufforstung ins Auge fassen. Beschwingten Gruss, hps
Peter Birett
02.12.2014 23:58
Ich bin fasziniert (und eigentlich sollte ich seit 1 Stunde schlafen ;-)
In den Filmen von Josiah Hunt und Mark Sission sehe ich wirklich gute Ideengeber und Grundlage für den Kon-Tiki. Tolle Umsetzung!
Was mich fasziniert, ist der Wasser-Einlauf zum Löschen des Feuers von unten her.
Um die Bio-Kohle zu beleben, kann ich mir gut vorstellen, nach dem Ablassen des seifigen Wassers (am besten gleich dabei Temperatur messen, 38°C wäre ideal, denn dann), den Kon-Tiki mit purem EMa aus einem nur höhergestellten 1qm Kanister (oder mit Lader hochgehoben) voll laufen zu lassen.
Das später wieder abgelassene EMa würde ich teilweise mit dem vorher abgelassenen seifigen LöschWasser vermischen, bevor es in den Garten vergossen wird. Den anderen Teil würde ich für die KüchenAbfall-Bokashi-Herstellung, Bio-Toilette verwenden oder in die GülleGrube schütten.
Ich bin gespannt auf einen Bericht, wie diese EM-getränkte TerraPreta-Kohle anders sich anfühlt, riecht, den Boden bereichert, als die bisher hergestellten Chargen.
Voll Freude und Begeisterung, Euer Peter
Werner Münzker
03.12.2014 07:16
Wenn das mit dem Verkohlen von dürrem Gras und Staudengestrüpp geht (und das nehme ich an), dann würde ich das noch vereinfachen:
Artikel ganz oben lesen, Gruben graben und das Material der Umgebung verkohlen. Dann mit Erde abdecken (Wasser wird Mangelware sein) und gut ist es.
Keep it simple and stupid!
Werner
hps
03.12.2014 16:56
Erdmeiler wären hier kurzfristig sicher die billigste Variante. Allerdings ist das Aufgraben der Löcher in der harte Erde unter sengender Sonne und ohne Maschinen ziemlich mühsam. Wohningegen man die Meiler von Ort zu Ort rollen kann. Wir arbeiten teilweise mit einer Kombination von Erdmeilern mit konischem Metalring zur Verbesserung der Verbrennungsdynamik. Da gibt es eine ganze Reihe von Kombi-Lösungen je nach Situation vor Ort.
Claudia Malfer
03.12.2014 16:43
.....seltsam............ohne es zu wissen, hab ich mit in den letzten Monaten angewöhnt, meinen Kaminofen "verkehrt rum" aufzustapeln, also von oben her abzubrennen, den dicksten Klotz am Boden. Meine Erfahrung, dass
es wider Erwarten super funktioniert und viel weniger rußt und Rauch entwickelt.
Und die Idee meines Vorredners Peter Birett, in das auf 38 ° abgekühlte Löschwasser Effektive Mikroorganismen (EM) einzubringen find ich auch hervorragend, weil damit die positiven Bakterien gleich ein gutes Zuhause bekommen, was zur Vererdung und Düngung gut ist und auch in der Tiernahrung
heilsame Wirkung hat.
Euer Forschen und Wirken macht Freude und Hoffnung - ein guter Beitrag zur Rettung unserer Erde, unserer Natur. clima
DanielG
03.12.2014 22:18
Meine Frau hat in Udon Thani / Thailand Landwirtschaftsland. Die Herausforderungen in der Landwirtschaft sind gewachsen. Grosse Waldflächen wurden in den letzten 20 Jahren abgeholzt, der Boden ist sandig und schnell ausgetrocknet, Nährstoffe werden bei heftigen Regen schnell ausgewaschen, das gespeicherte Wasser in den Seeen wird für die schnell wachsende Stadt selber gebraucht und immer mehr Bauern haben zu wenig Wasser für die Landwirtschaft in der Trockenzeit...
Permakulturkonzepte und mit einfachen Mittel Pflanzenkohle herzustellen werden der sehr armen Bevölkerung dort sicher helfen!
Ich bleibe dran!
Frank Strie
04.12.2014 04:49
Nun möchte ich mich doch auch gleich mal melden.
Wie schon alle zuvor, so möchte ich Hans-Peter Schmidt auch ganz herzlich gratulieren.
Es ist faszinierend wie ein Schritt dem nächsten folgt.
Kaum hatte ich Anfang Juli das Video von Paul & Hans-Peter gesehen war mir klar, dass damit ein großer Schritt in der Weiterentwicklung gelungen war.
Die Rohrleitung und 2" / 50mm Schnellkupplung und 2" Schlauchleitung mit dem gezielten Designer Aktivierungstee - Löschflüsssigkeit im 1m3 Containertank auf der Ladepritsche funktioniert super und so schnell oder langsam wie der Bioköhler es wünscht.
Wir haben hier 'under Down Under' in Tasmanien, Australien seit August schon einige Mengen verschiedene Pflanzenkohlen mit unseren KON-TIKI-TAS kilns hergestellt.
Quellwasser, Hühnertee, Schweinegülle, mit und ohne Molasse.
Bisher haben wir
Weinranken, Haselnussruten, Obstbaumäste und Zweige, Nadelholz, Zypressenrinde, kleine Zweige und Baum Nadeln, Akazien - Wattle verkohlt.
Je feiner und dünner das Material, um so schneller die Verarbeitung / Verkohlung aber auch die konstante, gleichmäßige Zufütterung.
Sofern genug Biomasse vor Ort bereit liegt, kann eine Person 2 Kon-Tiks gleichzeitig beschicken. Man sollte dann auch 2 Tanks mit Löschflüssigkeit bereit haben.
Je nach Einwirkungsdauer kann man dann mit einer keinen Motorpumpe die Flüssigkeit wieder abpumpen und nochmals verwenden.
In den nächsten Wochen folgen Versuche mit stacheligen Unhölzer wie Gorse, das allein in Tassie so ~100,000ha überzogen hat.
http://www.environment.gov.au/biodiversity/invasive/weeds/publications/guidelines/wons/pubs/u-europaeus.pdf
Da werden dann 4 oder 5 Kilns zeitversetzt - (wie im Chor bei einem Kanon) parallel angeheizt, mit einem Bagger gefüttert und dann abgelöscht.
Na dann werden wir mal sehen, wo das noch hingeht ...
Beste Grüße aus dem Sommer in Tasmanien
Frank Strie
Terra-Preta Developments
Schwabenforest Pty. Ltd.
Carsten
05.12.2014 23:05
Es ist eine faszinierend einfache und in sich schlüssige Technologie aus sehr guter Beobachtung, Überlegung und den Folgerungen daraus. Die Analogie zu den Pyrolyseöfen aus der Entwicklungshilfe in Afrika, Haiti und Indien (Sampada) ist sehr gut sichtbar. Besonders faszinierend die Qualität des Feuers und nach dem Quenchen von unten die Qualität der Biokohle. Es gibt sicherlich ein sehr großes Interesse an kleineren Kon-Tikis für Haus- und Kleingärten und die Entwicklungshilfe weltweit. Ich bin höchst gespannt auf die nächsten Mitteilungen. Die Verbreitung ist annehmbar lawinenartig und stimmt hoffnungsfroh.
Mit besten Grüßen
Gernot Heinrich
06.12.2014 09:40
Das ist eine großartige Methode um alle organischen Materialien, die wir bisher größtenteils für die Kompostbereitung verwendet haben, wie z.B. Baumhäckselgut, Strauchschnitt, Rebholz, Schilf vom Neusiedlersee, zuerst in
eine haltbarere, wertvollere Kohlenstoffform umzuwandeln und erst dann in einem weiteren Schritt der Kompostierung und nachfolgenden Beimpfung mit
unseren biodynamischen Präparaten zwecks "Informationsaufladung" zuzuführen. Wir haben ja auch in der Vergangenheit schon sehr positive Erfahrungen mit Komposteinsatz in den zum Teil schwer erodierten Hanglagen
mancher Weingärten gemacht und ich freue mich schon darauf Pflanzenkohle selber zu bereiten und den Boden noch mehr zu verlebendigen!
Alfons-E. Krieger
09.12.2014 05:26
Lieber Hans-Peter und Paul,
ich habe lange nicht mehr so einen interessanten Artikel gelesen.
Schön, dass Ihr uns in so einer klaren und logischen Weise Eure Gedanken / theoretischen Grundlagen und Schlussfolgerungen sowie praktischen Empfehlungen zu einer low tec (Volks-) Pyrolyseanlage mitgeteilt habt. Wegen der Schadstoffproblematik bei den (gefühlgeregelten) low tec Karbonisierungslösungen war ich kein Freund der do it your self Pflanzenkohleherstellungsanlagen.
Jetzt hast Du mich überzeugt, dass es Möglichkeiten gibt, diese Gefahren und Probleme zu lösen.
Leider wird die freiwerdende Prozesswärme, wie bei den technischen (Groß-) Anlagen noch nicht genutzt. Da wird Euch aber auch noch was einfallen – da ist noch was drin.
Aber bei den kleinen Anlagen ist das kein Problem, da man bei der Karbonisierung auch viel Spaß hat und es zum Beispiel mit einem Feuerritual oder als Partyfeuer als Feuerschalenersatz mit bleibender Pflanzenkohle nutzen kann und viele Herzen erwärmen und zum Beispiel Stockbrot backen kann.
Die Genialität liegt auch in dem recht simplen Quenchen mittels Wasserdampf - das auch technisch recht einfach zu bewerkstelligen ist.
Ich sehe eine ganz große Perspektive von kleinen Kon-Tikis für Haus- und Kleingärten und in der Entwicklungshilfe.
Ich selbst habe einen Bedarf an einen kleinen Kon-Tikis und werde mein letztes Geld nicht für einen Gartenhäcksler ausgeben, um meine zahlreichen Sonnenblumenstängel (an denen sich noch die Waldvögel laben) und perspektivisch Maisstängel, Maisspindeln und Strauch- und Obstbaumschnittmaterial mit den Kon-Tiki zu karbonisieren und meinen Gartenboden mit der Pflanzenkohle verbessern.
Viele liebe Grüße mit Wünschen eines gewaltigen Demokratisierungsaufschwunges
Alfons-Eduard Krieger
Ludwigsfelde
Leuenberger
11.12.2014 17:30
Seit ca. einem Jahr produziere ich mit dem PyroCook selber Pflanzenkohle. Ich koche dann meistens Wasser, da ich viel heisses Wasser brauche, um meine Bienenkasten usw. zu reinigen Die Kohle mische ich dem Kompost bei. Ich kompostiere nach der Handregel, d.h. heisskompostieren. So erhalte ich ein qualitativ gutes Substrat. Den Baum-und Strauchschnitt füttere ich zuerst den Kaninchen. So bleibt dann nur noch Holz übrig. Die Kaninchen müssen nie zum Arzt, und ich weiss was ich für Fleisch habe. Das kommt gut mit dem Kon-Tikis.
Freundliche Grüsse
Ernst Leuenberger
Sabine Koch
15.12.2014 13:42
Eure Webside hat mir ein Bekannter empfohlen. Ich bin begeistert wie einfach es ist, mit dem Kon-Tiki Pflanzenkohle herzustellen. Wir betreiben Weinbau in Steil- und Terrassenlagen bei Tübingen. Rebschnitt und Holz aus Rodungen von verbuschten Flächen haben wir bis jetzt meistens gehäckselt oder verbrannt. Aber nun würden wir gerne auch Pflanzenkohle daraus machen. Unser Dorfschmied könnte uns sicherlich einen Kon-Tiki bauen. Dazu würden uns die Baupläne interessieren. Gerne spenden wir dann auch einen Beitrag für die Weiterentwicklung des Kon-Tiki. Wir freuen uns auf eine Antwort…
Sabine Koch und Stefan Haderlein
Y.I.Morales
27.12.2014 22:15
Guten Tag Herr Hans-Peter Schmidt
Mich interessiert, ob Sie auch schon statt mit einer Konusform mit Pyramidenform, z.B. einer hexagonalen Pyramide "Pyra-Tiki" experimentiert haben.
Die Luftwirbel wären da zwar weniger harmonisch als bei einem Konus, aber da stelle ich mir einige Vorteile vor, die die Nachteile einer aus flächenbasiert hergestellten "Pyra-Tiki" überwiegen:
1. Minimale Technische Voraussetzung für die Herstellung, Blechschere (Autogen- oder Plasmaschneider bei dickem Blech), Schweissgerät oder Nietgerät plus Bohrmaschine.
(Keine massiven Walz-, Abkant- und Schermaschine nötig bei Verarbeitung von dicken Blechen)
2. 0% Verschnitt, Rest und Verlust bei rechteckigen Stahlblech als Rohmaterial möglich.
3. Ein faltbares Pyra-Tiki Design durch Scharnierverbund (genietet oder geschweisst)
4. Niedriger Transportaufwand und Kosten bei kompakt faltbarem Pyra-Tiki.
5. Faltbares Pyra-Tiki kann von einer Person transportiert und aufgestellt werden. Passt in einen Pkw.
6. Erzielung von Herstellungskosten bei Sammelbestellung bestimmt nicht nur unter knapp 3000 €, sondern weit unter 1000 € möglich.
7. "Do-it-your-self Pyra-Tiki set" bestehend aus vorgeschnittenen dreieckigem Stahlblech für Kunden mit Schweissgerät. (Einziger Herstellungsaufwand: Blech in Dreiecke scheren)
8. Demokratisch nicht nur Pflanzenkohle sondern auch Pyra-Tiki herstellbar. Dezentral anbietbar durch Schlossereien.. (^_^)
Noch was:
Wen schon eine Öffnung am Boden des Kon-Tiki vorhanden ist für späteres "Quenchen" bzw. aktivieren der Pflanzenkohle mit Wasser..
Die Öffnung kann man auch zu Beginn nutzen um Luft einzublasen um die erste Holzladung anzuzünden bis eine Glutschicht und eine eigene gute Luftzirkulation entsteht. Ein kleiner handlicher Bläser wirkt Wunder.
Freundliche Grüsse
Y.I. Morales
hps
31.12.2015 02:45
Vielen Dank für die Ideen zur Pyramidenform. Tatsächlich hat diese einige Vorteile und wir haben bereits einige selbst montierbare achteckige Kon-Tiki gebaut. Insbesondere haben wir diese Form hier in Nepal gewählt, da die Maschinen zum Biegen der Konusform nicht verfügbar sind. Wo die Maschinen zum Rundbiegen jedoch vorhanden sind, ist dies natürlich einfacher und billiger, da es nur eine Schweißnaht anstatt derer acht braucht.
Wir haben auch achteckige Kon-Tiki zum Zusammenschrauben gebaut, so dass sie als "flat-pack" verschickt bzw. transportiert werden können. Wenn man die Einzelteile in Serie mit entsprechenden computergestützten Maschinen bauen kann, ist dies sehr interessant, wo allerdings wie hier selbst Biegemaschinen nicht verfügbar sind, stößt das große Geschick der Handarbeiter bei 3mm Stahl an seine Grenzen. Ausserdem sind hier die feuerfesten Abdichtbänder nicht verfügbar, um die verschraubten Stöße zum Quenchen dicht zu bekommen. Da es Schweißgeräte und Flex quasi in jedem Dorf gibt, haben wir uns für Entwicklungsländer zu achteckigen, verschweißten Kon-Tiki entschieden.
Das Einblasen von Verbennungsluft durch das Wasserrohr am Boden funktioniert, braucht aber ein ziemlich kräftiges Gebläse zu Beginn.
Mehr über alternative Kon-Tiki Designs werden wir in einem nächsten Artikel vorstellen und diskutieren. Geplant für spätestens Ende Februar.
Frank Strie
01.01.2015 02:16
Also erstmals HAPPY 2015 - Beste Grüße und beste Wünsche für 2015 aus Tasmanien!
Da wir ja jetzt schon ein paar m3 Char hergestellt haben und dies mit verschiedenen Materialien und Stückgrößen, so lernt man ständig dazu.
The Burn-floor / Der Brennboden soll ja opimiert werden.
The Glow-zone / Die Glühzone sollte nach unseren Erfahrungen in der oberen Hälfte ablaufen.
Da gibt es dann auch die Möglichkeit der Wärmenutzung als Durchlauferhitzer - Wärmetauscher. Wir arbeiten dran.
Das neue Jahr wird bestimmt weiterhin spannend bleiben.
Watch this space!
Frank
Terra-Preta Developments
Schwabenforest Pty Ltd
Y.I.Morales
03.01.2015 09:09
Guten Tag Herr Hans-Peter Schmidt
Sie haben erwähnt das für die oktagonalen und verschraubten kon-tiki in Nepal keine hitzebeständigen Abdichtbänder fürs quenchen verfügbar sind..
Wie wäre es den statt dessen mit einer vor Ort hergestellten hitzebeständigen Abdichtmasse das man von innen oder noch besser auf die verschraubten Flächen appliziert?
z.B. aus einer Graphit-Ton/Lehm-Bitumen mischung?
Graphit (pulver) - macht Ton/Lehm hitzebeständig
Ton/Lehm - als Verbundmasse das festgebrannt wird.
Bitumen - als Porenverdichter und Kleber
Freundliche grüsse
Y.I. Morales
hps
04.01.2015 00:47
Am Bodenblech geht die Abdichtung mit gutem Kohle-Lehm recht gut, an den verschraubten Seitenwänden ist es schwieriger, aber Bitumen würde sicher gehen, aber dann ist der Vorteil der Verschraubbarkeit schon wieder hin, wenn man jedes Mal erst neu abdichten muss bzw. zum Demontieren die Dichtung aufschneidet. Es ist insgesamt einfacher, die Bleche zu einem oktagonalen Kiln zu verschweißen. Schweißgeräte gibt es überall und die Bleche könnte man vorgeschnitten liefern. Schönen Gruss, hps
Y.I.Morales
04.01.2015 08:26
Da fällt mir gerade ein...
Möchte selbst ein kon-tiki zusammen schweissen, aber hier in Südamerika hab ich grad nicht ne Biegemaschine um 3mm Blech zu biegen... Also nur Pyramidenform möglich.
Aber so viele lose Einzelteile exakt zusammen halten und dazu noch im korrekten Winkel ohne Verzug zusammenschweissen.. Sehr umständlich.
Da ich auch nur eine Flexmaschine habe um so dickes Blech zuzuschneiden...
Ich kann das doch auch alles nur aus einem einzigen Stückblech schweissen.
Anders als bei konischer form mit mind. zwei Teile (Boden + Seitenmantel).
Ich kann z.B. bei oktagonaler Trapezwanne 7 Ecken bei 3mm Blech mit der Flex nicht durchtrennen sondern auf die HALBE Wandstärke tief einschneiden inkl. eine Seite des oktagonalen Bodenblechs drannlassen.
So kann ich alles aus einem stück ohne biegemaschine exakt und einfach wie ein Papierwürfel zusammenfalten und hätte nur eine Ecke und ein Teil des Bodenblechs zu schweissen.
Evtl. danach die 7 gefalteten Ecken mit jeweils 5cm Schweissnaht von innen her am oberen Ende und Mitte Verstärken. Fertig.
PS:
Beim zusammen schraubbaren kon-tiki empfehle ich ähnlich vorzugehen.
7 Ecken + 1 Seite des Bodens mit durchgehenden Scharnierverbund und nur eine Ecke und Boden verschraubt.
So erspart man sich viel Zeit für die Montage und Demontage.
Freundliche Grüsse
Y.I. Morales
hps
04.01.2015 17:28
... wir hatten kein Problem, die acht Bleche sauber zu einem Oktagon zusammenzuschweißen. Das saubere Biegen der Bleche im richtigen Winkel hätte uns vor größere Probleme gestellt. Aber wenn es Ihnen gelingt, wäre es eine elegante Lösung. Bitte schicken Sie uns bald Bilder. Und viel Glück, hp
Hartmut Behrens
14.01.2015 12:56
Erstmal herzlichen Dank für diese ausführliche Information. Eine Frage des Gärtners: Gibt es ein einfaches Verfahren (ohne hohen Stromverbrauch), die immer noch recht harten Kohlestückchen zu zerkleinern, um sie dem Komposthaufen beizumischen?
hps
14.01.2015 16:47
In der Schweiz verwenden wir Gartenhäcksler, das geht etwa im gleichen Tempo, wie man den Kon-Tiki leer schaufelt. In Nepal haben wir herrlich robuste Gewürzmühle gefunden, das geht etwas langsamer, wird dafür aber sehr fein. Allerdings ist es mit dem Strom hier so eine Sache, der fließt meistens nur nachts. Also bauen wir an einer handgetriebenen Kohlemühle, ich werde einige Fotos dazu im nächsten Artikel bringen.
Thomas Schäffer
17.01.2015 07:24
Zunächst einmal Hut ab zu dieser Entwicklung! Ich bin begeistert und denke nach vielen Versuchen mit kleinen Tonnenkilns ernsthaft über einen Umstieg nach.
Meine Frage hat denn die Größe der Kohlestücke einen Einfluss auf deren Wirksamkeit? Sind Stücke in der Größe von 2 Würfelzucker nicht genau so wirksam wie feines Kohlepulver? Oder haben größere Stücke nicht sogar Vorteile im Boden?
Frank Strie
24.01.2015 10:43
Hallo Thomas Schäffer,
Man kann sich ja mal den Gedanken machen wie die Kompostwürmer und die Regenwürmer an der Pflanzenkohle nagen werden. Mit einem Shredder-Hammermühle habe ich heute in kurzer Zeit ca. 1m3 feuchte Biochar von bis zu faustgroßen Stücken auf optimale max.5mm zerkleinert.
Bisher habe ich immer die rohe Biochar im Komposthaufen verwendet und auch erst im Hühnerstall, in der Bodenstreu besonders dort wo die 15 "Federdamen" und der Hahn auf ihren Sitzstangen übernachten.
Die Mischung wird dann erst als Hühnertee - also als Flüssigdünger angesetzt und die Feststoffe anschließend im Komposthaufen eingeschichtet. Alles was nicht durch das Sieb geht kommt gleich wieder in den frischen Komposthaufen. Im Laufe der Jahre wird dann alles etwas feiner und die Mikroben und Bodenpilze haben immer eine gute Mischung.
Wie beim Hefe- und/oder Sauerteig, da ist viel Leben drin.
KompostKreis
16.02.2015 14:08
vielen Dank für den Artikel und die spannende Diskussion!
Beides werde ich denjenigen Teilnehmern meiner Workshops empfehlen, die größere Mikrovergaser bauen möchten.
Allerdings wird auch deutlich, welche Nebenerscheinungen mit zunehmender Größe einhergehen: Material-, Kapital-, sowie Werkzeug- und Zeiteinsatz steigen ebenso spunghaft an wie Gewicht und Sperrigkeit der Vergaser. Besonders schade finde ich, dass die Abwärme der Kon-Tikis bisher nicht genutzt wird.
Dabei ist es doch genial Suppe oder Kaffee zu kochen und als "Nebenprodukt" Holzkohle herzustellen. Mit der Fokussierung auf den Durchsatz an Holzkohle geht der Gedanke ineinandergreifender Kreisläufe doch wieder verloren. Meiner Meinung nach ist die Mehrfachnutzung der eigentliche Clou. Wer die wertvolle "Abwärme" ebenso nutzt wie die Holzkohle hat den nächsten Schritt getan. Wer dazu noch seinen Mikrovergaser aus vorhandenen Materialien selbst gebaut hat ist schon zwei Schritte weiter auf dem Weg zur Demokratisierung der Pflanzenkohleproduktion.
Herzliche Grüße aus Berlin,
Joachim Betzl
P.S.: Auf meinem Blog KompostKreis finden sich u.a. Anleitungen und Videos zu kleinen aber feinen Holzvergasern.
P.P.S.: Je kleiner bzw. feiner die verwendeten Holzstücke sind, desto leichter lassen sie sich anschließend auch zerkleinern.
Steffen Bläsing
18.02.2015 20:46
Um Holzkohle zu einem feinen Pulver zu zermahlen verwende ich einen
einfachen Betonmischer. Der wird mit der Holzkohle zur Hälfte gefüllt und
dann kommen etliche Kieselsteine dazu in verschiedenen Größen. Vor die Öffnung einfach Baufolie mit Draht befestigen (Mischer haben dort einen Rand).In zehn Minuten zermahlen die Steine die Holzkohle in feines Pulver.Mischer einfach in Schubkarre entleeren und die Steine über ein Sieb
wieder aussieben.
Holzkohle hab ich bisher in einem leeren Stahlfass gemacht nach der gleichen Feuermethode von oben nach unten brennen.
Viele Grüße
hps
20.02.2015 06:38
Liebe Frau Krause,
für solche Projekte wie das Ihre haben wir die Kon-Tiki Technologie ja ursprünglich entwickelt. Selbstverständlich werden wir Ihnen die Bauunterlagen dafür zur Verfügung stellen und sind über Erfahrungsberichte, Weiterentwicklungen und Anpassungen jederzeit dankbar. hp schmidt
Steivan
05.03.2015 20:48
Sehr geehrte Damen und Herren,
Ich habe mit grossem Interesse die Artikel von Ihrem Institut über die Produktion von Pflanzenkohle, vor allem über die Verwendung in der
Landwirtschaft gelesen. Imponierend ist der vielfältige Einsatz in Silage, Gülle, Tretmist und schliesslich zur Produktion von Terra Preta.
Wir bewirtschaften einen ca. 30ha. Biobetrieb auf 1400m.ü.m im Engadin. Bei uns fallen jährlich zwischen 4 bis 6 Tonnen Holzschnitzel an.
1.5-2 t werden für unsere Holzheizung verwendet, der Rest wird kompostiert. Mit dem Kon-Tiki Kegelmeiler zu Pflanzenkohle Herstellung
wäre eine viel bessere Lösung. Ich möchte gerne einen Kon-Tiki Kegelmeiler selber schweissen, dazu brauche ich Eure Unterstützung
mit technischer Zeichnung oder einer Bauanleitung.
mit freundlichen Grüssen
Steivan Meyer Etter
Bernhard T-M
09.03.2015 10:29
Hallo Hans-Peter Schmidt,
Ich hätte da eine sehr interessante Verbesserungsmöglichkeit. Konstruiere eine Kon-Tiki nach Berechnungen eines parabolischen Trichters Wirbeltechnik von Viktor Schauberger. Es wird aber sehr schwer umsetzbar sein (Biegung).
hps
09.03.2015 10:32
... aber wie wirft man dann die zu verkohlende Biomasse auf? Könnten Sie mal eine Skizze schicken, wie Sie es sich vorstellen?
Frank Strie
13.03.2015 20:38
Frage an Bernhard T-M
... parabolischer Trichter Wirbeltechnik von Viktor Schauberger?
oder sollte das der Hyperbolischer Schauberger-Trichter werden?
http://www.alles-wirbelt.de/versuche
..." Viktor Schauberger hat sich oft mit dem Einwirbeln von Flüssigkeiten, vor allem von Wasser, beschäftigt, da das seine Eigenschaften sehr verbessern soll. Der Wirbeltrichter muss hyperbolische Form haben und das Wasser wird tangential eingestrahlt, wie auf dem Bild schön zu sehen. Der Trichter ist aus Kupfer, da dieses Metall außerdem noch positive Auswirkungen auf die Pflanzen haben soll.
Nach Aussage des Teichbesitzers ist nach ca. vier Wochen Betrieb die Qualität des Wassers (kleiner Gartenteich) viel besser, es ist deutlich klarer geworden und die Teichbewohner, eine Anzahl Kois, fühlen sich pudelwohl."
Bernhard T-M
22.03.2015 10:05
Ja so in etwa. Wenn das bei Wasser sehr gut funktioniert, dann müsste es bei der Luft ebenso sein. Je weniger Wiederstände um so besser. Viel Luft in kürzerer Zeit, um so schneller wird der Vorgang bei der Verkohlung sein.
Harald Kaiser
24.03.2015 09:20
Hallo,
eine tolle Sache habt ihr da gemacht mit dem Kon Tiki.
Bezüglich der Holzkohleproduktion habe ich mir selber auch Gedanken gemacht, wie man das einfach machen könnte.
Ich dache dabei an eine Tonne mit Deckel, durch die in der Mitte ein Ofenrohr führt. Dieses Ofenrohr ist Teil eines sogenannten Rocket Stove Ofens, der in den USA sehr bekannt ist und dessen Hitzeabgabe trotz geringeren Brennmaterials doppelt so hoch wie unser europäischer Kanonenofen ist. Der R.St. besteht im Grunde nur auf Rohren oder Kanteisen in L- Form und hat am unteren waagrechten Teil wieder ein kurzes Stück Rohr schräg nach oben, das lediglich der Zuführung von kleinem Brennholz dient. Im Internet gibt es genug Videos dazu, wenn ihr das nicht kennen solltet, woran ich aber zweifle... Die Tonne kann in diesem Fall ja gleich voll angefüllt werden und mittels Deckel geschlossen werden. Der Deckel sollte einen Rohr oder Schlauchanschluss für die entstehenden Gase haben, mit denen man einen Generator zur Stromerzeugung betreiben könnte. Oder man führt die Gase dem Hitze erzeugenden Rocket Stove zu und verbrennt sie, was wahrscheinlich auch den Bedarf an Brennmaterial verringert. Was haltet ihr von dieser Idee?
Herzliche Grüsse
Harald Kaiser
PS: Der Kon Tiki erinnert mich sehr an ein großes Agnihorta Gefäß, nur das dieses eben 4 Kanten hat, statt der Rundung. Ich glaube das Funktionsprinzip ist aber das Gleiche.
Wittmann
03.04.2015 10:36
Hallo Herr H.Kaiser,
wir haben eine Tonne umgebaut mit Innenbehälter und Kohle + Pyrogas produziert. Das entstande Gas wird über einen Gasmotor mit Stromgenerator ( Klein- BHKW ) verbrannt und es wird Wärme und Strom dezentral erzeugt .
Laut BAFA wäre das BHKW, auch als Einzelmodell voll anmeldetauglich.
Kosten natürlich viel geringer als von Vaillant, Vissmann oder sonstigen Lobbyisten Firmen.
Bei Fragen bitte melden
Gruß
L. Wittmann
Friedrich Müller
21.04.2015 20:32
Guten Tag Hans-Peter Schmidt, Terra Preta für meinen Schrebergarten herzustellen betreibe ich das ganze Jahr über. Unterbrochen von einer Woche Alpenwanderung und einer Skiwoche. Da ist der Kon Tiki vor diesem herrlichen Panorama ein Traum!!
Ich habe einen Pyrolyseofen nach einem Video ‘eine kleine Farm’ verkleinert nachgebaut. Er braucht ganz trockenes Holz bestimmter Stückelung und arbeitet optisch und riechbar sehr rauchgasarm. Aber es ist auf einem rostigen Gefäß eine relativ große Flamme zu sehen und es knistert auch. Das assoziiert Verbrennung und das ist im Kleingartenverein verboten. Deshalb bin ich darauf aus die Pyrolyse als Kohlenstoffsenke neben der Kompostverrottung und dem traditionellen Grillen in Kleingärten zu legalisieren. Wenn das geschafft ist baue ich einen Kleingarten-Kon-Tiki. Diese Bauart passt auch besser für die Gemeinschaft um das Feuer. Aber zunächst: Wie viel des aus der Atmosphäre aufgenommenen CO2 wird bei Verbrennung,Verrottung, Pyrolyse und Grillen wieder abgegeben? Welche anderen Gase spielen auch eine Rolle? Wie sind die vier Vorgänge klimawirksam zu beurteilen? Beim Trennklo kann ich die Tür zumachen, den Pyrolyseofen sieht jeder. Ich schreibe von einem kleinen Garten: in Leipzig und auch anderswo gibt es viele davon.
Herzliche Grüße
Friedrich Müller
hps
21.04.2015 21:03
Nach Auskunft einiger Behörden wird der Garten Kon-Tiki als Grillfeuer akzeptiert und ist ja auch mit einem großen schwenkbaren Grill ausgestattet. Aber Gartengemeinschaften haben häufig ihre eigenen Regeln, da ist es sicher besser erst einmal eine Vorführung für alle Nachbarn zu organisieren und gleich noch mit erklären, wie die Kohle im Kompost und Trockenklo zum Vorteil für den Boden wird. Beim Kon-Tiki bleibt etwa die Hälfte des Kohlenstoffs der ausgänglichen Biomasse als Pflanzenkohle zurück, der größte andere Teil wird sauber verbrannt. Es entstehen auch (wie bei jeder Verbrennung) einige Spurengase wie Methan, Kohlenmonoxid, Stickoxid usw., aber sie sind nach unseren umfassenden Messungen sehr gering und auf jeden Fall nicht höher als die üblichen industriellen Pyrolys-, Vergaser und Verbrennungsanlagen. Wir werden die Ergebnisse der Emissionstest bei der Internationalen Biochar Tagung Ende Mai in Potsdam präsentieren und dann auch veröffentlichen. Bei sorgfältigem Betrieb des Kon-Tikis hat die Pflanzenkohle EBC Premiumqualität und kann auch zertifiziert werden. Schöne Grüsse und besten Dank für den Kommentar, Hans-Peter Schmidt
Böhmer
19.08.2015 17:48
Bisher war immer die Rede davon, dass die Holzkohle zu Staub zerkleinert werden soll um sie effektiv zu nutzen. In Ihren Beiträgen lese ich nichts davon, kann man also grobe Stücke verwenden?
Mit bestem Dank
Böhmer
hps
19.08.2015 20:01
Größere Kohlestücke schaden nichts solang genug feineres Material dabei ist, was in der Regel der Fall ist. Wenn wie mit dem Kon-Tiki das Herstellen der Pflanzenkohle so einfach ist, dass es weniger Mühe macht, sie herzustellen als sie zu zermahlen, dann nimmt man einfach ein bisschen mehr.
Ansonsten geht das Zermahlen recht gut mit Gartenhäckslern, je größer desto besser. Grüsse, hps
Hendrik
06.02.2016 21:40
Hallo,
ich habe mal ein wenig über den Namen Kon Tiki recherchiert.
Soweit ich es durch mehrere Internetseiten und auch wissenschaftliche Studien zu dem Thema lesen konnte ist nicht Kon Tiki (Qun Tiksi Wiraqucha) der Feuergott sondern sein Sohn Inti.
Kon Tiki wird als der Schöpfer der Zivilisation benannt. Das passt ja trotzdem sehr gut da die Kultur nur durch die Nutzung der Holzkohle (in der Terra Preta) zu einer Hochkultur und Zivilisation werden konnte.
Der Artikel sollte also ein wenig angepasst werden um keine, soweit ich es recherchiert und verstanden habe, falschen Infos zu verbreiten.
Ich überlege den Artikel mit Hilfe meiner Freundin ins Französische zu übersetzten. Gibt es da schon Leute die da dran sind?
Grüße, Hendrik
hps
07.02.2016 07:35
Vielen Dank, Hendrik, es stimmt, dass wir mit der Ausweitung der göttlichen Prädikate Kon-Tikis (Qun Tikis) auf das Feuer, die Geschichte etwas überstrapaziert haben. Aber insofern Qun Tiksi in der Mythologie auch als Schöpfer des Lichtes gilt, haben wir gemeint, dass zum Licht eben auch das Feuer gehört, aber ein richtiger Feuergott wie der hinduistische Agni ist er tatsächlich nicht. Aber als Schöpfergott wird er uns schon über die Schultern geschaut und die Hand geführt haben, als wir die uralte Verkohlungstechnik am offenen Feuer technisch ein bisschen weiterentwickelten.
Eine Übersetzung ins Französische wäre sicher sehr hilfreich für die leider noch immer sehr wenigen, die sich in Frankreich mit Pflanzenkohle beschäftigen.
Daniel Nägeli
28.07.2016 15:50
Hallo Hans-Peter Schmidt,
Wir haben einen grösseren Permakultur- und Natur-Garten (2000 qm) und ich veranstalte auch Führungen. Für den Gemüseanbau ist der Lehmboden mit vielen Steinen (Gletschermoräne) fast etwas zu schwer (und in letzter Zeit zu nass!). Gerne würde ich die Gemüsebeete mit Biochar anreichern. Die Versuche waren mehrheitlich positiv.
Vielen Dank für die Anleitung zum selber graben eines Kon-Tiki! Was ist der minimale Durchmesser für einen Erd-Kontiki? Geht es in einem Garten auch etwas kleiner als 2 m, oder ist er dann zu klein, um die Temperatur von 600° zu erreichen? Ich habe vor allem viel Heckenschnitt, z.T. stachlig. Offenbar gibt es ein Metall-Modell mit 1.20 m Durchmesser.
Beste Grüsse, Daniel
hps
29.07.2016 06:06
Der Kon-Tiki lässt sich ohne Weiteres verkleinern. Im Grunde kann man auch in einer Erbsendose nach dem Kon-Tiki Prinzip Kohle herstellen. Allerdings gilt trotzdem, dass je größer der Kon-Tiki, desto stabiler ist die Verkohlung, was daran liegt, dass die Energiezufuhr und der Energieaustausch zum Trocknen und Pyrolysieren frischer Biomassen umso größer ist, je mehr Biomasse im Kon-Tiki verschwelt. Ein weiterer Vorteil der Größe ist, dass gerade stachliger Strauchschnitt nicht zerkleinert werden muss.
Erd-Kon-Tiki mit einem Durchmesser von 80 cm funktionieren noch immer sehr gut, wenn Platz für 1m20 ist, wäre es besser. Entscheidend ist, dass die ganze Sache praktisch bleibt und angepasst ist an die räumlichen Voraussetzungen und die Menge der monatlich anfallenden Biomassen.
Schöne Grüsse, Hans-Peter
Ralph Ritter
30.07.2016 20:19
Hallo Herr Nägeli,
seit ca. 8 Jahren hat mich das Thema „Kohlenstoffkreislauf“ nicht mehr losgelassen, und im Jahr 2010 kam dann noch meine Entdeckung des Themas „Biokohle“ (heute Pflanzenkohle genannt) dazu.
Zuerst alles theoretisch, jedoch kam die Praxis bald in der Form einer alt hergebrachten Kompostierung im kleinen, in ausschließlich mit Handarbeit zu bewältigendem Maßstab hinzu.
Die Praxis ermöglicht mir mein Hausgarten von ca. 800 qm zu pflegen und zusätzlich einige Schrebergartenparzellen von insgesamt 1500qm, wo ich hauptsächlich Gemüse für unsere Selbstversorgung und Futter für zwei Milchziegen und einiges Federvieh in ökologischer Weise anbaue.
Das Ithaka-Journal ist seither (allerdings in unregelmäßigen Abständen) mein Begleiter und „Mutmacher“, jedoch war ich immer nur Zaungast.
Daß ich nun über den Zaun gestiegen bin, hat den Grund, daß ich vor 3 Wochen meine erste eigene praktische Erfahrung mit der Pflanzenkohleproduktion gemacht habe und nun fast zeitgleich Ihr Beitrag hier zu lesen war. Inspiriert wurde ich durch einen Beitrag hier im selben Thema etwas weiter oben, als jemand berichtete, wie er Pflanzenkohle in einer alten Badewanne hergestellt und mit Urin abgelöscht hat.
Ich hatte nun keine Badewanne zur Hand, jedoch einen alten Waschkessel, der früher auf jedem Bauernhof zur notwendigen Grundausstattung für die große Wäsche oder zum Hausschlachten gehörte. Der Kesseleinsatz hat ein Fassungsvermögen von 150 Liter, ist rund und etwas konisch mit einem oberen Innendurchmesser von ca. 90 cm.
Meinen dritten Pyrolyse-Durchgang möchte ich nun folgendermaßen zusammenfassen:
In der Umgebung gesammeltes trockenes Astwerk bis max. 2 cm Durchmesser (3 Kübel je 200 l) habe ich in ca. 90 min in diesem Kessel pyrolysiert, in dem als Ergebnis ca. 100 Liter Pflanzenkohle übrig geblieben sind. Abgelöscht habe ich mit 30 l Regenwasser. Später wurde dies in einem Freifallmischer unter Beigabe von einigen runden Feldsteinen zerkleinert.
Verwendet habe ich den größten Teil der Pflanzenkohle als ca. 10 vol-%ige Beimischung zu einem frisch aufgesetzten Kompost und kann bereits jetzt bestätigen, daß die anfängliche Temperatur um mind. 5 Grad höher ausfällt (ca. 75 Grad Celsius), als ich es bisher gewohnt war.
Einen weiteren Teil der Pflanzenkohle verwende ich als Zugabe zur Einstreu im Ziegen-, Hühner- und Gänsestall. Auch stelle ich zum „Naschen“ für die Tiere jeweils ein Töpfchen bereit.
Was auch mein Problem hierbei ist:
1. Kann ich auf diese Art überhaupt eine ausreichende Temperatur erreichen, oder erzeuge ich doch mehr Schadstoffe für die Tiere und den Boden, als mir lieb ist? (Wenn es in einer Erbsendose auch funktionieren soll, dann ist meine Frage bereits beantwortet?)
2. Gibt es Erfahrungen oder Richtwerte bei der Ausbeute der Pflanzenkohle gegenüber dem Ausgangsmaterial? Bei mir waren es ja 600 l lockeres Astwerk zu 100 l dichter gelagerte Pflanzenkohle.
Viele Grüße, Ralph Ritter.
hps
31.07.2016 05:41
Haben Sie vielen Dank, sehr geehrter Herr Ritter, für Ihren ausführlichen Bericht, der sicher vielen Mut macht und auf die rechte Idee kommen lässt, selbst die Kohle herzustellen, die sie/er in ihrem/seinem jeweiligen Garten oder Hof benötigt.
Die besonders gute Qualität der Kohle wird durch das luftoffene Prinzip der Herstellung garantiert. Insofern bei der Pyrolyse hinreichend Sauerstoff mit der entstehenden Kohle reagieren kann, werden etwaige Schadstoffe wie Teere oder PAKs (als Oberbegriff wird hierfür Kondensate oder Flüchtige Kohlenwasserstoffe (VOC) gebraucht) zu unschädlichen Stoffen abgebrannt. Die Kohleporen werden also durch den Sauerstoff und am Ende durch den Wasserdampf beim Ablöschen gereinigt und die Oberflächen der Kohle funktionalisiert (die Oberflächen werden reaktiver und die Adsorptionsfähigkeit und Nährstoffaustauschkapazität nehmen zu).
Das Entscheidende für eine gute Qualität der Kon-Tiki Kohle, egal ob im Erdloch, in der Badewanne, im Design Kon-Tiki oder in der Erbsendose ist es, für einen möglichst gleichmässigen, heissen Flammenteppich über der zu verkohlenden Biomasse zu sorgen. Sobald es anfängt zu qualmen, ist nicht mehr genügend Hitze und Sauerstoff vorhanden, was die Qualität der Kohle negativ beeinflusst und auch nicht gut für die Atmosphäre sein lässt. Also: Kein Rauch, dann ist auch die Kohle gut. (Achtung: bei Verwendung von feuchten Biomassen steigt Wasserdampf auf, der ist natürlich nicht schädlich und ist nicht mit Rauch zu verwechseln).
Die Ausbeute an Kohle hängt vor allem von der Stückigkeit und Trockenheit der verwendeten Biomassen ab. Bei sehr trockenem, dünnen Strauchmaterial haben wir Umsatzraten von über 25% (von Trockenmasse der Biomasse zu Trockenmasse der Kohle) erreicht, bei feuchtem, dickastigem Holz sind es manchmal nur knapp 15%. Aufs Volumen gerechnet ergibt dies etwa ein Reduktionsverhältnis von 2 - 3 Teilen Biomasse zu 1 Teil Pflanzenkohle. Geht man davon aus, dass Ihre 600l lockeres Astwerk mehr Luft als Ast hatten, ergaben die 200 - 300 l Biomasse rund 100 l Kohle, was gut zur Theorie passt.
Beste Grüsse, Hans-Peter
Ralph Ritter
13.11.2016 16:32
Vielen Dank, Herr Schmidt,
für Ihre Bestätigung dafür, dass ich (wenn auch nur in sehr kleinem Rahmen meiner Möglichkeiten) bei meiner Pflanzenkohleherstellung auf dem richtigen Weg bin.
In meiner Herstellungskette auf dem Weg zur Terra Preta stellt sich momentan für mich als größtes Problem die Zerkleinerung der doch relativ großen Kohlestücken (Ursprung war ca. 2 cm dickes Astwerk) dar:
• Mehrmaliges Einfüllen in den Freifallmischer, zusammen mit einigen Feldsteinen,
• Aussieben mit einem engmaschigen Sandsieb,
• Siebrückstand wieder in die Mischbirne, das gleiche Spiel von vorn!
Um hier etwas effektiver arbeiten zu können, wäre es für mich hilfreich zu wissen, was die optimale, bzw. maximale Korngröße der einzelnen Kohlestücken ist, um dann nicht unbedingt hunderte von Jahren warten zu müssen, bis sich die größeren Stücken im Boden durch Verwitterung selbst noch weiter zerkleinert haben.
Gibt es bezüglich der Korngröße Richt- bzw. Erfahrungswerte?
Viele Grüße, Ralph Ritter.
hps
13.11.2016 16:59
Wenn wir größere Kohlestücken haben (aus Astmaterialien) schaufeln wir die Kohle durch einen Gartenhäcksler. Das geht schnell und ergibt gute Korngrößen. Bei der Verkohlung sonstiger Ernterester (Blätter, Zweige, Stroh etc.) ersparen wir uns das Zerkleinern gänzlich. Wenn über 50% der Kohle aus feinerem Material besteht, stören einige größere Stücke nicht, sie lockern den Boden auf und speichern auch Wasser und Nährstoffe. Es gibt bisher keine Nachweise, dass besonders fein gemahlene Kohle für den Boden oder Kompost besser sei. Die hervorragenden Resultate, die wir im Artikel über die Wurzelapplikation in Nepal veröffentlicht haben, wurde alle mit ungemahlener Kohle erzielt. Die Indianer am Amazonas, die die Terra Preta erschaffen haben, hatten auch keine Hammermühle.
Schönen Gruss, Hans-Peter
Jürgen
31.03.2017 13:10
..nach meinem Besuch auf der Finca Autarca auf La Palma versuche ich mich jetzt in Deutschland auch mit der Terra Preta.
Die Holzkohle ist in der Tat der schwierigste Faktor. Nicht nur weil teuer, ich möchte auch nicht meine Gartenabschnitte "wegwerfen" und Holzkohle über weite Strecken transportieren lassen.
Erste Versuche mit "drei" Eimern - Ausseneimer als Kamin, Inneneimer für die groben Holzstücke und dann, wenn es brennt, stelle ich einen Honigeimer, -gefüllt mit Sägemehl- mit 4 kleinen Löchern im Deckel in die Glut. Das dampft erst, dann kommen kleine Flammen heraus und wenn die erloschen sind,ist im Honigeimer feinste Holzkohle. Die Groben Holzkohlestücke werfe ich nach dem Erkalten in den Gartenhäcksler, bevor sie auf den Kompost kommen...
Das sind nur kleinste Mengen. Meine derzeitige Wunschvorstellung wäre eine schöne Feuerschale, wie es sie zu Hauf gibt, ca. 70-100 cm Durchmesser, aber eben in der tieferen Kon-Tiki-Kegelform. Gibt es so etwas irgendwo zu kaufen, bzw. wie lässt sich so etwas selbst herstellen? Welche Eisendicke wird empfohlen?
Lieben Gruß vom Bodensee
Jürgen
hps
04.04.2017 18:11
Für die kleinen Kon-Tiki Feuerschalen genügt eine Stahldicke von 2 mm, die größeren sollten 3 mm haben. In der Schweiz stellt Markus Koller (Gais) sehr schicke und funktionstüchtige Kon-Tiki in allen Größen her. In Deutschland macht es die Firma Söhlmetall in Obertaufkirchen.
Günter Böhm
26.02.2019 19:43
Hallo, Herr Schmidt,
1. Kohle zerkleinern
in Winterbach hat im Herbst letzten Jahres Herr Dunst aus Kaindorf einen Vortrag über Terra Preta gehalten mit großer Resonanz.
Jetzt haben wir erstmal mit der Kon-Tiki-Methode Pflanzenkohle hergestellt. Jetzt aber heißt es, die Pflanzenkohle wirke am besten, wenn sie sehr kleinteilig ist. Unsere Kohle ist aber auf Grund der verwendeten Zweige grobteiliger. Manchmal bis 4 cm. Wie bekommt man sie klein wie Sand? Darüber findet man in ihren Informationen nichts. Können sie uns helfen? Gibt es da eine Maschine?
2. Beurteilung der Terra Preta
Nach dem Vortrag von Herrn Dunst schrieb ich an unseren Ministerpräsidenten Kretschmann, was er von Terra Preta halte. In den Anlagen schicke ich ihnen den Schriftwechsel. Einiges widerspricht dem, was wir von Herrn Dunst von seinem Vortag und auch aus den Videos über seine Humustage erfahren haben. Nach Darstellung der Landesregierung ist Terra Preta für tropische Gegenden sinnvoll, für uns nicht unbedingt. Zu viel Humus würde sich auch negativ auswirken. Wegen der Nitratauswaschung hat Herr Dunst anscheinend die Österreichischen Behörden überzeugt.
Wie beurteilen sie das?
Mit freundlichen Grüßen Günter Böhm, Friedrichstr. 6, D 73650 Winterbach
hps
03.03.2019 22:46
Lieber Herr Böhm,
Zum Zerkleinern von nicht allzugroßen Mengen Pflanzenkohle eignet sich am besten ein Gartenhäcksler. Allerdings spielt es für die Bodenapplikation keine so große Rolle, ob dass alles gleichmässig klein gemahlen ist. Einige größere Stücke schaden nicht. Lieber ein bisschen mehr nehmen, als ewig viel Zeit mit dem Mahlen verlieren. In Nepal haben die Frauen anfangs die Kohle mit dem Hammer kleingehauen. So hätte sich das nie in die Praxis durchgesetzt. Später haben wir die Kohle einfach so verwendet, wie sie aus dem Kon-Tiki kam (+ organische Nährstoffbeladung). Funktioniert genauso gut.
Vielen Dank auch für Ihre Bemühungen beim Ministerpräsidenten. Leider fremdelt seine Partei mit Innovationen im landwirtschaftlichen Bereich. Die Politik zieht nach, wenn die Realität sich verändert. Letzteres ist unsere Aufgabe.
Herzlich, Hans-Peter Schmidt
Werner Münzker
05.03.2019 05:38
Die Zerkleinerung funktioniert auch sehr gut in einer normalen Betonmischmaschine.
Kohle hinein, ein paar (sehr) große Kiesel dazu und einschalten.
Nach einiger Zeit ist die Kohle nur mehr Staub, je nach Feuchtigkeit vorher auch ein schwarzer Brei.
mario
13.10.2019 18:16
Hallo zusammen, hat jemand eine Meinung dazu oder Erfahrung damit, die Kohle direkt mit Urin oder Brennesseljauche abzulöschen? Das würde doch das Trocknen und wieder Aufladen ersparen??? Danke für ein Feedback. viele Grüsse Mario
hps
13.10.2019 19:36
Ja, genau, das Ablöschen mit flüssigen organischen Nährstoffen ist die beste (und übliche) Methode.
mario
14.10.2019 12:35
Vielen Dank für die Info. Da ich in den Unterlagen immer von Wasser als Ablöschmittel gelesen habe, war ich unsicher, ob es evtl. Nachteile mit sich bringt, wenn man direkt mit flüssigen Nährstoffen ablöscht. Bis jetzt habe ich immer mit Wasser abgelöscht, dann die Kohle getrocknet und erst dann geladen.
Wir (Gartenbaubetrieb) experimentieren fleissig und verköhlern unser Schnittgut regelmässig im Kon Tiki.
herzlichen Dank für die inseresanten Infos und Texte.
viele Grüsse mario
Theresa
27.11.2019 10:46
Guten Tag, ich habe eine Frage zum Erd-Kon-Tiki:
Bei unseren letzten Pyrolysefeuern im Oktober/November bei nasser kalter Witterung war es kaum möglich, das Feuer trotz sorgfältig aufgeschichtetem Kamin in Gang zu bringen bzw. eine ausreichende Temperatur zu erreichen. Das habe ich daran erkannt, dass der Prozess ewig dauerte (doppelt so lange wie bei Trockenheit) und es stark qualmte. Hat damit jemand Erfahrung? Kann es sein, dass bei feuchtem Erdreich ein starker Kühlungseffekt von den Seitenwänden ausgeht? Bringt es da was, den Erd-KonTiki abzudecken? Oder gibt es eine andere Möglichkeit, auch im Winter darin Pflanzenkohle herzustellen? Z.B. vorher ein "normales" Feuer zum Trocknen im Erd-KonTiki zu machen?
Außerdem würde ich gern wissen, wie die Meinung der Fachleute dazu ist, wenn das Ablöschen vom ErdKontiki mit Urin-angereichertem Wasser etc. erfolgt: Versickert dann nicht sehr viel nährstoffreiches Wasser in der Erde? Oder werden die Nährstoffe von der Kohle aufgenommen?
Viele Grüße aus Hessen und herzlichen Dank für die Möglichkeit, hier Fragen zu stellen!
Theresa
hps
27.11.2019 12:39
Sehr geehrte Frau Biermann,
Die Erdfeuchte eines winterlichen Kon-Tikis trocknet bei der Feuerung sehr schnell ab. Das Hauptproblem in Ihrem Fall wird vermutlich sein, dass die verwendete Biomasse (Holz?) wohl zu feucht war und vielleicht waren auch die Durchmesser der Holzstücke zu gross, wodurch die Trocknung im Feuer verzögert ist. Versuchen sie es doch noch einmal mit trockenen Zweigen, dann wird auch der winterliche Erd Kon-Tiki sicher nicht mehr rauchen. Mit freundlichen Grüssen, Hans-Peter Schmidt
Peter Hurni
19.11.2021 21:16
Guten Tag
Ich produziere mit einem Kontiki Pflanzenkohle und möchte diese im Kuhstall einsetzen. Die Kohle wird mit Wasser gelöscht und ist dann mit Wasser vollgesogen. Muss ich sie damit sie im Stall mit Gülle geladen wird vorher trocknen oder kann ich sie direkt aus dem Kontiki brauchen?
Herzliche Grüsse und besten Dank für die Antwort
Peter
hps
11.12.2021 10:32
... es ist sicher sinnvoll, die Pflanzenkohle vorher abtropfen zu lassen, aber trocknen muss man die Kohle nicht. Sie wird trotzdem die Nährstoffe aus der Gülle aufnehmen. Viel Erfolg, Hans-Peter