Autos als Kohlenstoffsenken
von Hans-Peter Schmidt & Nikolaus Foidl
Eine Druckversion des Artikels kann unter diesem Link heruntergeladen werden.
.Kohlenstoff erhaltende Waldholznutzung
Der europäische Wald ist insbesondere durch den Klimawandel stark gefährdet. Allein in den beiden Jahren 2018 und 2019 gingen in Deutschland über 150 Millionen Kubikmeter Holz durch Borkenkäfer- und Sturmschäden verloren. Die beim Verrotten des Holzes freigesetzte Menge an biologisch gebundenen Kohlenstoff entspricht etwa 10% der jährlichen CO2-Emissionen Deutschlands. Um die Schäden zu kompensieren, müssen Millionen neue Bäume gepflanzt werden. Doch neben der zweifellos wichtigen Aufgabe, neue Wälder anzulegen und Lücken zu schließen, wird es zur immer wichtigeren nationalen Aufgabe, die vorhandenen Wälder zu schützen und Kohlenstoff erhaltende Holznutzungen zu entwickeln.
Fällt man einen Baum und nutzt das gesamte Holz des Baumes, um daraus ein Material zu gewinnen, in dem der vom Baum aufgenommene Kohlenstoff langfristig gespeichert bleibt (z.B. einen Dachbalken, einen Schiffscontainer aus komprimiertem Holz oder Pflanzenkohle), und wächst während dieser Zeit der Holznutzung an der gleichen Stelle im Wald ein Baum nach, so hat man schließlich die doppelte Menge CO2 aus der Atmosphäre entzogen (der Kohlenstoff im neu herangewachsenen Baum plus der Kohlenstoff im Baumaterial, das aus dem gefällten Baum gewonnen wurde). Wird das Baumholz jedoch nicht als Industriematerial genutzt, sondern verbrannt oder man lässt es im Wald verrotten, so ist die Kohlenstoff-Bilanz im günstigsten Fall neutral. Dies aber erst nach ungefähr 70 Jahren, wenn der gefällte, gehäckselte und verbrannte Baum wieder nachgewachsen ist.
Nur wenn der Kohlenstoff, den der Wald durch die Bäume der Atmosphäre entzogen hat, dauerhaft in Materialien oder als Pflanzenkohle im Boden gespeichert wird, kann der Wald das Potential seiner Klimadienstleistung (C-Senkenleistung) voll ausschöpfen. Daher müssen dringend und rasch neue Holznutzungsformen entwickelt und industriell skaliert werden. Um das derzeitige und künftig zu erwartende Schadholz in einer Weise zu nutzen, die verhindert, dass es zu massiven Quellen neuer Treibhausgasemissionen wird, muss es dem Wald entzogen und in dauerhafte Industrieprodukte transformiert werden.
Auch wenn das Verbrennen von Biomasse zur Gewinnung von Strom und Wärme staatlich gefördert wird, weil es als erneuerbare Energie eingestuft wird, so zerstört doch jede Verbrennung einen natürlichen Kohlenstoffspeicher. Für das Klima ist das Verbrennen von Baum- und Strauchholz grundsätzlich erst einmal ebenso schädlich wie das Verbrennen fossiler Bodenschätze (Searchinger et al., 2018). Zur Rettung des Klimas sollte nicht nur das Verbrennen fossilen Kohlenstoffs, sondern ebenso das Verbrennen von Biomasse (ohne CCS) unterbunden werden, um die Biomasse stattdessen für den Aufbau von Kohlenstoffsenken in Form von Materialien zu verwenden.
Holz ist nicht nur ein Kohlenstoffspeicher, sondern eines der nobelsten und vielfältig nutzbarsten Rohstoffe der Erde. Im Grunde lässt sich aus Holz quasi alles herstellen, was bisher der Petrochemie (Erdöl basierte Chemie) vorbehalten war, sei es Plastik, Pharmaka, Kautschuk oder Batterien. Mit der neuen Technologie der Holzkomprimierung können Holzmaterialien nun auch Stahl, Beton, Kohlefaserverbundstoffe und sogar Glas ersetzen.
Komprimiertes Holz ist fester und stabiler als Stahl
Eine neue technische Methode erlaubt es, Holz so zu verdichten, dass sich beliebig formbare Bauteile herstellen lassen, welche eine höhere Druck- und Biegefestigkeit aufweisen als Titanstahl und Kohlefaserverbundstoffe (Song et al., 2018). Bei dem Prozess werden Holzbretter zunächst in einer alkalischen Lösung (z.B. NaOH – Na2SO3) gekocht, wobei über die Hälfte der Hemizellulose und des Lignins aus dem Holz herausgelöst werden. Übrig bleiben Zellulose-Nanofasern, die sich sodann komprimieren lassen. Durch das Verdichten der Zellulosefasern entstehen zwischen den Molekülketten der Zellulose Wasserstoffbindungen, wodurch die Zellulosefasern einen extrem festen Verbund untereinander eingehen. Nachdem das Holz also in der ungiftigen Lösung gekocht wurde, wird es in eine entsprechende Bauteilform gelegt und unter Dampfeinfluss bei 100°C mit etwa 5 MPa (50 Atmosphären) komprimiert. Das Volumen des Holzes schrumpft dabei um das etwa Fünffache.
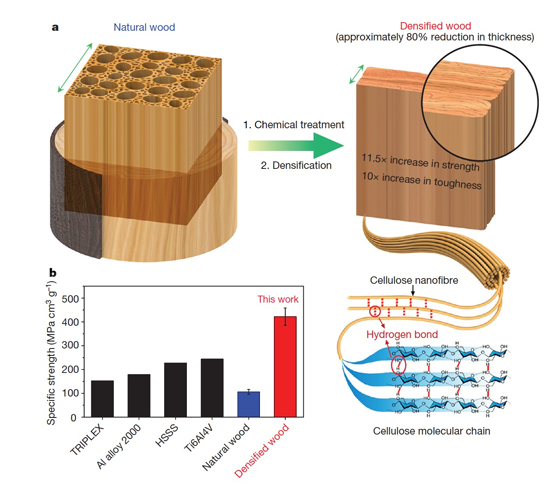
Das komprimierte Holz ist ein extrem dichtes, stabiles, kratzfestes, wasserabweisendes Material. Bei geeigneter Lackierung nimmt das komprimierte Holz kein Wasser auf, so dass es auch zu keiner mechanischen Verformung kommt. Das komprimierte Holz ist korrosionsbeständig und ein guter Wärmeisolator. Das Material hat neben der deutlich höheren Festigkeit und des weitaus geringeren spezifischen Gewichts weitere wesentliche Vorteile gegenüber den üblicherweise verwendeten Metallblechen im Karosseriebau.
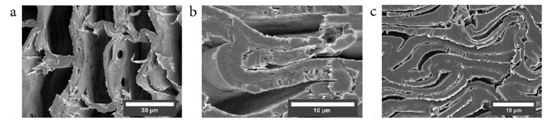
Die Materialeigenschaften und Festigkeiten des komprimierten Holzes würden es ermöglichen, dass sowohl Karosseriebleche von Autos und deren Innenverkleidung als auch das Fahrgestell und sogar die Felgen aus diesem biologischen Material hergestellt werden könnten.
Als Ausgangsmaterial für komprimiertes Holz kann Buche ebenso wie Fichte, Pappel oder jedes andere Stammholz des globalen Waldes verwendet werden (Song et al., 2018).
Nutzung der Holzabfälle
Borke, Sägespäne und Verschnittholz, die bei der Verarbeitung der Bäume für die zu komprimierenden Holzplatten anfallen, können pyrolysiert werden. Bei diesem Prozess entsteht Pflanzenkohle und Pyrolyseöl (Schmidt et al., 2018). Die Pflanzenkohle könnte feingemahlen als 2-5%iger Zusatz in die Textilien der Innenausstattung von Autos eingewebt werden, was ein angenehmes Innenklima begünstigt. Pflanzenkohle und Pyrolyseöl könnten aber ebenso auch im Straßenbau als Asphaltzusatz verwendet werden, wobei der Kohlenstoff, der ursprünglich vom Baum aus der Atmosphäre entzogen worden war, viele Jahrhunderte stabil im terrestrischen System gebunden bliebe.
Die ausgekochte Hemizellulose könnte zur Herstellung von Nylon oder Treibstoffen, und das Lignin z.B. zur Kunststoffherstellung verwendet werden.
Das Auto als fahrende Kohlenstoffsenke
Um das enorme Potential von Holz abzurufen, braucht es industrielle Vorreiter, die die Chance holzbasierter (Kohlenstoff speichernder) Materialien erkennen und als Marktvorteil nutzen. Ein Autohersteller zum Beispiel, der bereit ist mit den Konventionen von Stahl und Plastik zu brechen, könnte mehr noch als mit dem simplen Wechsel von Benziner auf Stromer die Fahrzeugkultur der Zukunft gestalten und zugleich ein enormes Marketingpotential aufbauen.
Für die Herstellung eines Autos werden je nach Größe, Bauart und Schönrechnung zwischen 5 und 10 t CO2 emittiert. Würde man das Auto vom Fahrgestell über die Karosserie bis zur Innenausstattung mit biogenen Materialien bauen, könnte bei einem Leergewicht von 1.5 t und unter Abzug der nicht biogenen Materialien (Motoren) sowie des Aufwandes zur Materialbereitstellung eine Kohlenstoffsenke von über 1 t CO2eq entstehen. Das Auto würde also über seine Lebensdauer den Kohlenstoff speichern, der ursprünglich von einem Baum aus der Atmosphäre entzogen worden war.
Das (nicht rostende) Auto würde somit zu einer mobilen Kohlenstoffsenke. Alles komprimierte Holz, das im Auto verbaute wurde, kann am Ende des Lebenszyklus des Autos unter geringem Energieaufwand gehäckselt und dann pyrolysiert werden, wobei der größte Teil des Kohlenstoffs ebenso wie bei der Pyrolyse der Holzabfälle langfristig erhalten bleibt. Die dabei entstehende Pflanzenkohle ist ein wertvolles Bodenhilfsmittel in der Garten- und Landwirtschaft, oder kann zur Verbesserung der Isolation in Baumaterialien verwendet werden. Der Kohlenstoff, der in den Holz basierten Materialien des Autos gespeichert war, bliebe also noch für weitere Jahrhunderte im Boden oder weiteren Produkten gespeichert. Er würde nicht wieder als CO2 in die Atmosphäre gelangen. Die C-Senke des Autos könnte also zu einem großen Anteil langfristig erhalten bleiben.
Würde mit dieser biobasierten Technologie der derzeitige Fuhrpark von 1.25 Milliarden Autos ersetzt werden, könnten damit rund 1 Gt CO2eq sequestriert werden, was ca. 3% der weltweiten CO2eq-Emissionen entspricht.
Stand der Entwicklung
Der Prozess zur beschriebenen Komprimierung von Holz ist seit über 15 Jahren bekannt. Allerdings wurden erst in den letzten knapp fünf Jahren die wissenschaftlichen Grundlagen für einen industriellen Einsatz geschaffen. Hier sind insbesondere die Forschungen an der University of Maryland, der KTH Stockholm und der ETH Zürich zu nennen (Li et al., 2016; Frey et al., 2018; Song et al., 2018). Es gibt bereits eine Reihe von Patenten, die die Technologie schützen. Industrielle Anwendungen sind unseres Wissens bisher noch nicht realisiert. Grundsätzlich sind die technischen Hürden für die Umsetzung und Skalierung dieser Technologie überschaubar. Für ein Pilotprojekt zur Konstruktion eines rezyklierbaren C-Senken-Autos sollten bei entsprechender Kapazität für Forschung und Entwicklung die Grundlagen der Technologie weit genug entwickelt sein.
Frachtcontainer und weitere C-Senken-Produkte aus komprimiertem Holz
Als Pilotprojekt wäre der Herstellung eines Autos aus komprimiertem Holz ein weltumspannendes Medienecho sicher. Wie einst bei Tesla würde es nicht nur das Potential der neuen Technologie vor Augen führen, sondern als Vorreiter den Weg dafür weisen, dass die moderne Konsumgesellschaft nur dann ihren Lebensstandard halten kann, wenn quasi alle Industrieprodukte zu Kohlenstoff-Senken oder komplett rezyklierbar werden. Auf dem Weg zur C-Senken-Industrie liegen freilich eine ganze Reihe einfachere Industrieprodukte als Autos, die schneller und mit geringeren Entwicklungskosten zu verwirklichen wären. Die Konstruktion und die Herstellung von Frachtcontainern soll im Folgenden als Beispiel dienen.
Ein 40 Fuß-Frachtcontainer aus Stahl wiegt ca. 4 t und emittiert bei dessen Herstellung durchschnittlich 8 t CO2eq. Aufgrund der insbesondere vom Seewasser beschleunigten Korrosion beträgt die Lebensdauer der Container nur 15 Jahre (Buchanan et al., 2018). Für das Einschmelzen und Rezyklieren des Stahls fallen dann weitere 1.2 t CO2eq an (Obrecht & Knez, 2017). Würden die Container anstatt aus Stahl aus komprimiertem Holz hergestellt und würde dabei das Gewicht um 25% reduziert, so würde das Holz jedes Containers 1.5 t Kohlenstoff (5.5 t CO2eq) als C-Senke enthalten. Durch die Gewichtsersparnis könnten zudem rund 20% der für den Frachttransport benötigten Treibstoffe eingespart werden, was über 15 Jahre bei heutigem Treibstoffverbrauch pro 40 Fuß-Container ca. 30 t CO2eq entsprechen würde (Buchanan et al., 2018). Insgesamt würde also die Verwendung von komprimiertem Holz für den Bau von Frachtcontainern rund 45 t CO2eq pro 40-Fuß-Container einsparen. Bei den weltweit derzeit 18,6 Millionen Frachtcontainern (10, 20 und 40 Fuß- Container) ergäbe dies ein Einsparungspotential von ca. 650 Millionen t CO2eq, dies sind immerhin gut 1,7 % der derzeitigen globalen Treibhausgas-Emissionen.
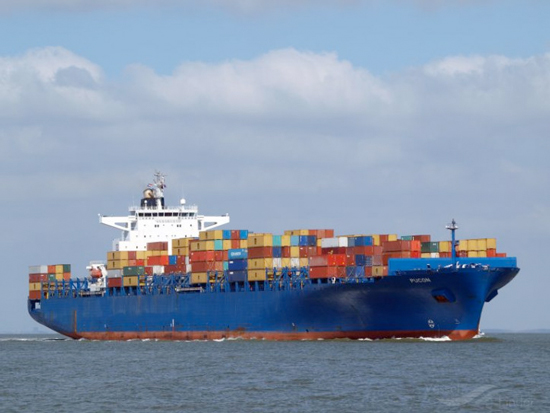
Die Frachtcontainer aus komprimiertem Holz wären aber nicht nur robuster und zugleich leichter, sondern hätten zudem noch weitere Vorteile: Während die Stahlcontainer mit toxischen Rostschutzmitteln auf Basis von Chrom, Phosphor und Blei bestrichen sind, benötigt das komprimierte Holz, das durch seine extreme Verdichtung ohnehin max. 3% Wasser aufnimmt, lediglich pflanzliches Öl zur Imprägnierung. Da das Holz nicht rostet, lässt sich auch mit deutlich längeren Lebenszyklen als jene 15 Jahre der Stahlcontainer rechnen. Am Ende des Lebenszyklus kann das komprimierte Holz wie im Fall der Autos zu Pflanzenkohle und Bioöl verarbeitet werden, womit die C-Senke des Materials erhalten bliebe.
Ein weiterer Vorteil der Container aus komprimiertem Holz wäre die viel bessere Wärmeisolation, womit erhebliche Mengen Energie für die Kühlung, insbesondere bei Lebensmitteltransporten, eingespart werden könnte. Forscher der Universität Maryland haben ein komprimiertes Holz entwickelt, welches Sonnenlicht in einer Art und Weise reflektiert, dass dabei sogar das Oberflächenmaterial aktiv gekühlt wird (Li et al., 2019). Umgebungsstrahlung wird dabei von dem komprimierten Holz in mittelwellige Infrarotstrahlung umgewandelt, wodurch die Oberfläche Wärme abgibt. Während die Stahlcontainer sich in der Sonne schnell aufheizen, würden die Holzcontainer gerade auf den durch den tropischen Gürtel verlaufenden Frachtlinien über 50% Energie für Kühlung sparen (Li et al., 2019).
Schiffscontainer sind ein hervorragendes Bespiel dafür, wie die Transformation der (Schwer-)Industrie hin zu biogenen Materialen, die zugleich C-Senken sind, in der Regel mit zahlreichen weiteren Vorteilen einhergeht. Von Computergehäusen, den Rahmen für Solarpanels und von Windräder bis zu korrosionsbeständigen Armierungen von Brücken und Hochhäusern aus Beton, komprimiertes Holz könnte zum Motor der biobasierten Wirtschaft werden, wobei jedes neue Produkt zur dauerhaften C-Senke würde. Nur so kann es gelingen, die Kohlenstoffbilanz des Planeten wieder auszugleichen.
Das Motto des nächsten Jahrzehnts muss also lauten: Transformation von Industrieprodukten zu biogenen C-Senken.
Weitere Informationen
Das Ithaka Institut hat ein Interview mit einem der Pioniere dieser Holztechnologie, Nikolaus Foidl, aufgenommen, welches unter folgendem Link angehört werden kann: http://ithaka-institut.org/ithaka/media/doc/wood.mp3
Ein sehr gut zusammenfassender Artikel auf Englisch erschien kürzlich in Scientific American und lässt sich unter folgendem Link lesen: https://www.scientificamerican.com/article/stronger-than-steel-able-to-stop-a-speeding-bullet-mdash-it-rsquo-s-super-wood/
Eine Druckversion des Artikels kann unter diesem Link heruntergeladen werden.
Literatur
Buchanan CA, Charara M, Sullivan JL, Lewis GM, Keoleian GA. 2018. Lightweighting shipping containers: Life cycle impacts on multimodal freight transportation. Transportation Research Part D: Transport and Environment 62:418–432. DOI: 10.1016/J.TRD.2018.03.011.
Fang, C.-H., Mariotti, N., Cloutier, A., Koubaa, A. & Blanchet, P. Densification of wood veneers by compression combined with heat and steam. Eur. J. Wood Wood Prod. 70, 155–163 (2012).
Frey M, Widner D, Segmehl JS, Casdorff K, Keplinger T, Burgert I. 2018. Delignified and Densified Cellulose Bulk Materials with Excellent Tensile Properties for Sustainable Engineering. ACS Applied Materials & Interfaces 10:5030–5037. DOI: 10.1021/acsami.7b18646.
Hill, C. A. et al. The water vapour sorption properties of thermally modified and densified wood. J. Mater. Sci. 47, 3191–3197 (2012).
Kutnar, A. & Kamke, F. A. Compression of wood under saturated steam, superheated steam, and transient conditions at 150 °C, 160 °C, and 170 °C. Wood Sci. Technol. 46, 73–88 (2012).
Laine, K. et al. Measuring the thickness swelling and set-recovery of densified and thermally modified Scots pine solid wood. J. Mater. Sci. 48, 8530–8538 (2013).
Laine, K., Segerholm, K., Wålinder, M., Rautkari, L. & Hughes, M. Wood densification and thermal modification: hardness, set-recovery and micromorphology. Wood Sci. Technol. 50, 883–894 (2016).
Li Y, Fu Q, Yu S, Yan M, Berglund L. 2016. Optically Transparent Wood from a Nanoporous Cellulosic Template: Combining Functional and Structural Performance. Biomacromolecules 17:1358–1364. DOI: 10.1021/acs.biomac.6b00145.
Li T, Zhai Y, He S, Gan W, Wei Z, Heidarinejad M, Dalgo D, Mi R, Zhao X, Song J, Dai J, Chen C, Aili A, Vellore A, Martini A, Yang R, Srebric J, Yin X, Hu L. 2019. A radiative cooling structural material. Science (New York, N.Y.) 364:760–763. DOI: 10.1126/science.aau9101.
Navi, P. & Heger, F. Combined densification and thermo-hydro-mechanical processing of wood. MRS Bull. 29, 332–336 (2004).
Obrecht M, Knez M. 2017. Carbon and resource savings of different cargo container designs. Journal of Cleaner Production 155:151–156. DOI: 10.1016/J.JCLEPRO.2016.11.076.
Schmidt H-P, Anca-Couce A, Hagemann N, Werner C, Gerten D, Lucht W, Kammann C. 2018. Pyrogenic carbon capture and storage. GCB Bioenergy. DOI: 10.1111/gcbb.12553.
Searchinger TD, Beringer T, Holtsmark B, Kammen DM, Lambin EF, Lucht W, Raven P, van Ypersele J-P. 2018. Europe’s renewable energy directive poised to harm global forests. Nature Communications 9:3741. DOI: 10.1038/s41467-018-06175-4.
Song J, Chen C, Zhu S, Zhu M, Dai J, Ray U, Li Y, Kuang Y, Li Y, Quispe N, Yao Y, Gong A, Leiste UH, Bruck HA, Zhu JY, Vellore A, Li H, Minus ML, Jia Z, Martini A, Li T, Hu L. 2018. Processing bulk natural wood into a high-performance structural material. Nature 554:224–228. DOI: 10.1038/nature25476.
Dr. Armin Siepe
28.12.2019 06:49
Lieber Hans-Peter, ein toller und innovativer Artikel, danke!! In Gänze wegweisend & unterstützenswert!
Bitte erlaube mir aber doch, an einer Stelle einen Neben-Aspekt zu korrigieren: 2. Absatz im Artikel: "Lässt man Baumholz im Wald verrotten, ist die Kohlenstoffbilanz im besten Fall neutral."
Allein schon das Wort "verrotten" suggeriert Negatives, Unnützes.
Tatsächlich aber ist das Totholz ungemein wertvoller Lebensraum, für Pilze, Käfer, Insekten, Nahrungskette (Biodiversitäts-Strategie = Arten-Vielfalt, gegen Arten-Sterben, nach Alt- & Totholz-Konzepten Wald, FSC-Siegel u.v.m.).
Aus Sicht der Klimabilanz aber: Dabei baut sich wieder Humus im Waldboden auf, der durch eine permanente Holz-Nutzung ansonsten überwiegend entzogen würde. (Allein nur Laub- und Schwachholz-Verbleib im Wald erhält allenfalls den Humus-Pool, oft nicht einmal das.) Die Kohlenstoffsenke 50-60% C im Humus ist ja bekannt, ebenso die vielfachen weiteren Nutz- und Lebensraum-Wirkungen eines gesunden, Humus-reichen Bodens im Wald (und nicht nur dort)! Der Boden könnte dank Totholz Humus Klimagas-Senke sein, ist unter Nutzung derzeit allermeist aber Klimagas-Quelle!
Auf die Spitze getrieben wird eine nur sektorale Betrachtung in einer jüngst weit verbreiteten Pressemitteilung des Fachverbands Pflanzenkohle mit ähnlicher Aussage (in top-agrar u.a. Medien) - Zitat:
"Momentan liegen 17 Millionen Tonnen Holz in den Wäldern ... Sie verwittern ungenutzt und geben dadurch Kohlenstoff ab. Diese unglaubliche Menge an Material könnte zu sehr guter Pflanzenkohle verarbeitet werden. Dazu brauchen wir neben den nötigen technischen Anlagen auch die Rückendeckung und das Verständnis aus der Politik, was Pflanzenkohle wirklich leisten kann.“
Diese Empfehlung ignoriert die oben genannten und weitere wesentliche Zusammenhänge. Sie verstößt auch gegen Kriterien des EBC-Siegels (für Leser: Europäisches Biokohle Certificat, Grundlage für Pflanzenkohle- Herstellung und -Nutzung). Sie riefe, würde sie denn umgesetzt, zum Wald- und Humus-Plündern auf. Möge sie uns, der Forst-, Klima- und Bodenschutz-Politik erspart bleiben.
Gerade wir, die wir Natur- und Umwelt-Zusammenhänge ganzheitlich denken wollen, müssen uns stets bemühen, die mono-thematische und sektorale Brille abzulegen, so weit wir eben vermögen. Ithaka tut das in beeindruckendem Maße!!!
In diesem Sinn Danke für stetes, beeindruckend-engagiertes Wirken, alles Gute, jeden Erfolg und persönliches Wohlergehen weiter auch im Neuen Jahr 2020!
Herzlich Armin
-----------------
Dr. Armin Siepe
Büro SchwarzErde
Lindenplatz 3
D-76185 Karlsruhe
hps
28.12.2019 12:37
Lieber Armin,
Vielen Dank für den wichtigen Hinweis, den wir in dieser Diskussion nicht vergessen dürfen. Totholz hat im Wald eine enorm wichtige Funktion und ist nötig, um das Waldsystem in gesunder Balance zu halten. Aus Sicht der Kohlenstoffbilanz - und darauf bezog sich der Satz im Artikel - verursacht das Verroten von Baumholz sogar mehr Treibhausgase als das kontrollierte Verbrennen, da im Rotteprozess auch Methan entsteht. Das heißt freilich nicht, dass alles Totholz entfernt werden müsste. In Wäldern, die unter Naturschutz stehen, bleibt ja auch alles Totholz im Wald. In Wirtschaftswäldern aber gibt es keine absolute Notwendigkeit, mehr als einen biologisch notwendigen Prozentsatz an Totholz zu belassen. Klimaschutz ist nun einmal ein Kompromiss, der immer wieder zwischen den natürlichen und den anthropogenen Kohlenstoffkreisläufen ausgehandelt werden muss. Ohne Waldbewirtschaftung lässt sich die Treibhausgasbilanz nicht neutralisieren, selbst wenn die Verbrennung von fossilen Bodenschätzen bis 2050 auf Null zurückgefahren würde. Allerdings lässt sich aus der Waldbewirtschaftung nur dann ein Klimanutzen ziehen, wenn die Biomassen zu kohlenstoffspeichernden Materialien transformiert werden, und wenn weder der Wald noch der Humus weniger werden.
Herzlich, Hans-Peter
Dr. Armin Siepe
28.12.2019 19:23
Lieber Hans-Peter,
herzlichen Dank für Deine rasche Antwort! Wir sind uns einig, die Totholz- und Kohlenstoff-Vorräte in Waldböden zu erhalten, wo möglich auszubauen. Wälder unter Naturschutz, die Du nennst, in denen das Totholz grundsätzlich verbleibt, sind z.B. die Bannwälder in Baden-Württemberg. In denen (aber auch nur in denen) ist jede Nutzung, also auch Entnahme von Totholz verboten. Nun haben diese Wälder in B-W allerdings nur einen Flächen-Anteil von 0,22 %! Wir können uns bestimmt einigen, dass dieser geringe Anteil keinen flächendeckenden Humusschutz im Wald insgesamt bewirken kann!
Im Übrigen ist ja eben hier die Entnahme von Totholz verboten – also diese Wälder haben die von mir angesprochenen, auch kritisierten Empfehlungen zur Restholz-Entnahme aus dem Wald eben nicht gemeint.
Die Empfehlungen zur Restholzentnahme meinen vielmehr die Wirtschaftswälder. Hier wird aber ja sowieso das Nutzholz in großem Umfang entnommen, also ein erheblicher Teil des Kohlenstoffs bereits exportiert. Ich sprach ja nicht gegen Waldbewirtschaftung an sich - ganz bestimmt auch für den Klimaschutz. Meine Warnung gilt der Empfehlung, nun auch noch das restliche, bisher verbleibende Holz ganz oder in Teilen zu entziehen – zum Schaden der Boden- und Humusbildung, des Arten- und Biotopschutzes.
Die Deutsche Anpassungsstrategie an den Klimawandel nennt im Hinblick auf Wald-Böden das Ziel: „Schutz der ökologischen Leistungsfähigkeit der Böden durch die Erhaltung der organischen Substanz, Umsetzung standortangepasster Landnutzungsstrategien zur Verringerung negativer Effekte durch Veränderungen in der Boden- und Humusbildung.“
Die Europäische Forststrategie formuliert in dieselbe Richtung: „Bestehende Kohlenstoffbestände sollen geschützt und ausgebaut und neue Kohlenstoffbestände angelegt werden.“
FSC-zertifizierte Wälder wiederum legen eine „betriebliche Biotop- und Totholz-Strategie“ fest.
Ich weiß von meinen Forst-Kontakten, dass Totholz ganz gezielt aus diesen Strategien und Gründen im Wald belassen wird. Was wir heute in Zeiten der Intensiv-Nutzung im Wald noch haben, ist also (allenfalls !!!) der von Dir genannte "biologisch notwendige Prozentsatz an Totholz" (vielleicht eher nur knapp!). Da sind keine Riesen-Überschüsse mehr für Pflanzenkohle oder Ähnliches. Dem Anliegen der Forstverwaltung würde ein Aufruf also nicht gerecht, das (notwendige!) Restholz aus Klimaschutzgründen nun doch wieder zu entziehen.
Meine Aussagen sehe ich also konform mit den offiziellen Wald- und Forst-Strategien. Wir sollten also wesentlich differenzierter argumentieren, als eben nur aus der einen, sektoralen Sicht. Die hat uns schon bei vielen Themen des Natur- und Umweltschutzes in – durchaus vermeidbare - Konflikte geführt. Pflanzenkohle - für die ich mich einsetze - hat genug Widerstände. Diese hier brauchen wir nicht.
Herzlich Armin
Hermann Schuster
29.12.2019 21:58
Hallo Herr Schmidt
Ich habe den Beitrag „Autos als Kohlenstoffsenken“ mit Begeisterung gelesen, und mir das Interview angehört. Welche Möglichkeiten es gibt, Holz als Ausgangsproduckt zu verwenden, gleichzeitig den Kohlenstoff dauerhaft und sinnvoll zu speichern. Wenn ich das richtig verstanden habe, dann kann man nur astfreies Stammholz, einzelne Holzstücke oder Bretter zu hochwertigen Materialen verdichten. Meine Überlegung zu einer weiteren Möglichkeit wäre der Einsatz als Dachziegel. Damit könnte man die kurzen Stammstücke zwischen den Astreihen verwerten. Durch Ankohlen der Dachziegel würde die Haltbarkeit und Entflammbarkeit weiter erhöht werden.
Grüße und viel Erfolg bei den Aufgaben im neuen Jahr
Hermann Biobauer aus Österreich
hps
29.12.2019 22:07
Lieber Hermann,
Dachziegel wären tatsächlich eine weitere hervorragende Möglichkeit. Ich gehe davon aus, dass auch als Spänen verdichtete Holzmaterialien hergestellt werden können, aber das muss erst noch gezeigt werden. Das Torrefizieren/Ankohlen von Holz ist eine weitere wunderbare Möglichkeit, Holz dauerhaft haltbar zu machen, womit eben auch die C-Senkenkapazität gesteigert würde.
Holzschutz durch Oberflächen-Torrefizierung ist übrigens ein anderer Artikel, den ich schon seit langem einmal schreiben möchte.
Beste Grüsse und Dank für den Kommentar, Hans-Peter
Anton Bischof
12.01.2020 13:14
Hallo Herr Schmidt
Ein wirklich sehr interessanter Beitrag mit enormem Potential
Trotz aller Euphorie möchte ich drei Dinge anmerken:
1. Ich würde das Wort "ungiftig" bei den Laugen weglassen oder durch unbedenklich ersetzen.
2. Bei der Beschreibung über die Herstellung fehlt mir der Energieaufwand für das Kochen und Dämpfen, welcher sich natürlich je nach Brettstärke durch die unterschiedlichen Kochzeiten extrem verändert und
3. ist es zwar genial, dass man zu entsorgende Teile zerhäckseln und verkohlen kann, aber wenn diese zuvor gegen Wasseraufnahme lackiert waren ist das nicht mehr so unproblematisch.
@Interview: Wenn Sie die Flasche innen leicht antoasten, erreichen Sie einen noch viel größeren Effekt als in Barriques :-)
Mit freundlichen Grüßen
Toni Bischof
hps
12.01.2020 14:02
Vielen Dank für die wertvollen Anmerkungen.
1) Hinsichtlich der Laugen ersetze ich das "ungiftig" gern durch "unbedenklich". Allerdings ist genau das im Auge zu behalten. Zwar sind die beiden bisher verwendeten Laugen tatsächlich unbedenklich, aber wie man die Industrie kennt, werden hier sicher noch ganz andere Laugen getestet werden, um den Prozess zu optimieren, und da sollte man dann genau darauf schauen, dass keine Umweltbelastungen auftreten.
2) Die Energiebilanz muss natürlich in die Gesamtbilanz einberechnet werden. Wir haben das bisher nur überschlagen und ableiten können, dass der Energieaufwand im Vergleich zum Energiegehaltes des Holzes gering ist, entscheidend wird dann die industrielle Umsetzung und wie im konkreten Fall die Energie bereitgestellt wird.
3) In den meisten Fällen sollte eine Imprägnierung mit natürlichem Öl genügen. Sollten spezielle Lacke verwendet werden, muss natürlich untersucht werden, welche Schadstoffe während der Pyrolyse daraus entweichen können.
Besten Dank und Gruss, Hans-Peter Schmidt
Uwe Thomas
02.02.2020 13:06
Hallo allerseits :)
ich frage mich, ob Hanf/zellulose sich wohl auch wie Holzzellulose zu komprimierten "Holz" be- und verarbeiten lässt.
Herzliche Grüße
Uwe
hps
02.02.2020 13:21
Das frage ich mich auch, gehe aber davon aus, dass es funktionieren sollte. Miscanthus, Switchgras, Bambus, Hanf - die C-Effizienz wäre deutlich höher als die von Bäumen.
jakob
04.04.2020 21:57
Der Artikel enthält sehr viel wertvolle Information, geht jedoch meiner Meinung nach zu wenig auf Herkunft des Holzes ein. Es gibt sogar einen Wiederspruch: heimische Wälder schützen und zugleich mehr Bauholz fördern? Ich glaube nicht.
Selbst wenn es möglich wäre dem Wald nicht durch das Gerät zu schaden und man die Auswirkungen auf Flora und Fauna in Grenzen halten könnte: Durch massenhaftest Abtransportieren des Holzes (und damit einhergehende Unterbindung einer lokale Zersetzung) muss doch der Waldboden extrem leiden, oder etwa nicht?
Vielen Dank für den Artikel und beste Grüße,
Jakob
hps
05.04.2020 07:54
Dem stimme ich uneingeschränkt zu. Aber wenn man all das Holz, das derzeit für sogenannte Bioenergie verbrannt wird, durch materielle Nutzung zu C-Senken macht, könnte man sowohl die heimischen Wälder schützen als auch mehr Bauholz erzeugen.
Die Nutzung von Wäldern als C-Senke sollte selbstverständlich mit Schutz von Wald und Biodiversität einhergehen. Hier gibt es den Unterschied zwischen Natur- und Nutzwäldern und vor allem die Kombination von Land- und Fortswirtschaft als Ackerforst, wodurch mehr nutzbare Biomasse für C-Senken erzeugt wird als durch reine Nutzwälder.
Werner
29.08.2020 11:20
(etwas Abseits der oberen Thematiken -aber wichtig für mich)
In Mitteldeutschland (auch oder gerade) an starken Hanglagen entstehen durch den Befall sehr viele Brachen.
Gibts es hier sinnvolle Möglichkeiten diese für die Zukunft
mit den Euch bekannten Möglichkeiten,
auch unter kostengesichtspunkten resilienter zu machen.
Die 2 Gespräche mit Förstern endeten immer mit Achselzucken.
hps
29.08.2020 22:58
Ja, die gibt es natürlich unzählige Möglichkeiten. Pflanzen sind Solarpanels und Kohlstoffsauger. Und es gibt, egal wie erodiert und trocken ein Boden ist, immer eine pflanzliche Lösung. Das Achselzucken der Förster heißt nur, dass sich sich nicht auf die Lehrbücher von vor 30 Jahren verlassen können. Aber es ist auch klar, dass solche Lösungen sich nicht einfach von Marktkräften lösen lassen, es braucht ein gesellschaftliches Engagement (Steuergelder und Weitsicht).
Noch sind die Weichen nicht gestellt, und der Klimazug rast schon heran, aber die Natur wartet nur auf die helfende Hand.
Herzliche Grüsse, Hans-Peter
Angela Franke
12.10.2020 18:05
Wenn Griechenland und Italien einen großen Teil ihrer Wälder in ihren Schiffen verbaut haben, aber auch beim Häuserbau und Heizen, dann frage ich mich, wie man diese Vielzahl an Holznutzungen eigentlich mit einem wirklich nachhaltigen Umgang mit Wäldern gestalten will. Mir scheint das eher auf diese Art Greenwashing wie Biodiesel oder Mais für Biogas hinaus zu laufen. Wo sollen denn die Unmengen Holz herkommen, wenn wir glauben unseren Lebensstil beibehalten zu können, nun allerdings mit Holz als Baustoff?
Wir haben inzwischen eine Sandkrise wegen der Bautätigkeit. Unsere Wälder schwinden ohnehin in rasantem Ausmaß und neue Holzplantagen sind kaum ein Beitrag zur Artenvielfalt und wohl auch nicht zum Klimaschutz, denn Bäume brauchen doch mehrere Jahrzehnte um zu wachsen und junge Bäume speichern auch kaum CO2.
https://de.wikipedia.org/wiki/Entwaldung_in_römischer_Zeit
Ich bin da sehr skeptisch um ehrlich zu sein.
hps
12.10.2020 18:15
Die Skepsis ist völlig berechtigt. Und allein die Nutzung von Holz wird das Klima nicht retten können. Worum es aber in einem ersten Schritt unbedingt gehen muss, ist der Stopp des Verbrennes von Holz zur sogenannten Bioenergiegewinnung. Bei der Verbrennung von Holz wird das aufgenommene CO2 unverzüglich wieder in die Atmosphäre ausgestoßen, während bei der Holznutzung der Kohlenstoff ausserhalb der Atmosphäre gespeichert bleibt. Auch im Alten Rom wurde 90% des Holzes verbrannt, die Materialnutzung war nicht der Hauptgrund der Entwaldung. Die entwaldeten Landschaften sind aber nicht nur die römische Macchie, sonder ziehen sich von Andalusien bis nach Shanghai quer durch Europa und Asien, da ist noch viel Platz für Aufwaldung.